
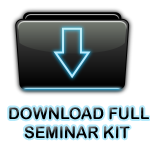
1.1 PRESENT SCENARIO
Induction motor, which is the important workhorse of all industries. Now days this machines are protected by oldest method that is protection is done by relay and circuit breakers. This type implemented in both static and electromagnetic type. These types of protection are done for protecting the machine for over current and over voltage .the main disadvantage is accuracy and reliability. It would sense the fault after few mille seconds; at that short period there is chance for damage in winding and other motor parts. Therefore there is need for accuracy and reliability of operation; therefore it is necessary for implementing new technique in order to protecting the machine due to high cost. There fore we go for the new method for diagnosing the fault occur in the induction motor. Fuzzy logic based fault identification system is one of recent technique with high accuracy and able to identify fault before it would damage the motor.
1.3 PROJECT DESCRIPTION:
The various fault that incurred in the three phase induction motor are identified and diagnose in the initial stage itself .due to involvement of fuzzy logic concept, the accuracy of fault detection get increased. The various fault that are occurred in the three-phase induction motor are unbalanced voltage, single phasing, blocked rotor, overload, over voltage, under voltage. The fault, which is above described, would damage the motor, which would occur in short period. Therefore fuzzy logic based algorithm are used to detect the fault and it is done with the help of micro controller PIC 16f877a.
The motor characteristics during several fault conditions are predicted using mat lab and the simulation result are shown below. The supply before fed to the three-phase induction motor is initially checked by the relay, which is micro controller fed relay. If there is no problem occurred in the supply it will fed to the motor.
The basic block diagram for this analysis is shown above. The supply initially fed to the motor is measured by the measuring circuit .The measuring circuit consist of the current transformer and potential transformer and the regulating circuit. From the regulating circuit it is connected to the micro controller the micro controller check the condition of the supply if there is any fault occurs it will give signal to the relay. Then the relay will automatically cut down the supply. The micro controller that has been incorporate here is the PIC 16f877a.
The Sensing Circuit Which Consist of CT&PT, measuring circuit and regulating circuit. Which initially senses and regulate the supply voltage and current and it give necessary input to the micro controller circuit .The micro controller execute the fuzzy logic algorithm based program which is to detect the various fault that has going to be occurred and it will sense, it will give necessary input to the LCD and relay circuit.
The fault which going to be occurred is initially detected and the corresponding fault are displayed in the LCD display, which is connected to the controller. Therefore this method of fault diagnosis is accurate way of control compare to the Past method and would avoid the damage of the motor
2.1 INDUCTION MOTOR
2.1.1 INTRODUCTION
Because of their wider applications in electromechanical energy conversion, mainly due to their low cost, reasonably small size, ruggedness, low maintenance, and operation with an easily available power supply, induction motors are the main workhorses of industrial prime movers.
2.1.2 INDUCTION MOTOR DESIGN
It has a major effect on the behavior and performance of an induction motor. Very often the details or class of design of a motor are not well understood or promoted.
2.1.2.1 STATOR DESIGN
The stator is the outer body of the motor, which houses the driven windings on an iron core. In a single speed three-phase motor design, the standard stator has three windings, while a single phase motor typically has two windings. The stator core is made up of a stack of round pre-punched laminations pressed into a frame, which may be made of aluminum or cast iron. The laminations are basically round with a round hole inside through which the rotor is positioned. The inner surface of the stator is made up of a number of deep slots or grooves right around the stator. It is into these slots that the windings are positioned. The arrangement of the windings or coils within the stator determines the number of poles that the motor has.
A standard bar magnet has two poles, generally known as North and South. Likewise, an electromagnet also has a North and a South Pole. As the induction motor Stator is essentially like one or more electromagnets depending on the stator windings, it also has poles in multiples of two. I.e. 2 poles, 4 poles, 6 poles etc.
The winding configuration, slot configuration and lamination steel all have an effect on the performance of the motor. The voltage rating of the motor is determined by the number of turns on the stator and the power rating of the motor is determined by the losses which comprise copper loss and iron loss, and the ability of the motor to dissipate the heat generated by these losses.
The stator design determines the rated speed of the motor and most of the full load, full speed characteristics.
2.1.2.2 ROTOR DESIGN
The Rotor comprises a cylinder made up of round laminations pressed onto the motor shaft, and a number of short-circuited windings. The rotor windings are made up of rotor bars passed through the rotor, from one end to the other, around the surface of the rotor. The bars protrude beyond the rotor and are connected together by a shorting ring at each end. The bars are usually made of aluminum or copper, but sometimes made of brass. The position relative to the surface of the rotor, shape, cross sectional area and material of the bars determine the rotor characteristics. Essentially, the rotor windings exhibit inductance and resistance, and these characteristics can effectively be dependant on the frequency of the current flowing in the rotor.
A bar with a large cross sectional area will exhibit a low resistance, while a bar of a small cross sectional area will exhibit a high resistance. Likewise a copper bar will have a low resistance compared to a brass bar of equal proportion.
Positioning the bar deeper into the rotor, increases the amount of iron around the bar, and consequently increases the inductance exhibited by the rotor. The impedance of the bar is made up of both resistance and inductance, and so two bars of equal dimensions will exhibit different A.C. impedance depending on their position relative to the surface of the rotor. A thin bar, which is inserted racially into the rotor, with one edge near the surface of the rotor and the other edge towards the shaft, will effectively change in resistance as the frequency of the current changes.
This is because the A.C. impedance of the outer portion of the bar is lower than the inner impedance at high frequencies lifting the effective impedance of the bar relative to the impedance of the bar at low frequencies where the impedance of both edges of the bar will be lower and almost equal.
The rotor design determines the starting characteristics.
2.1.2.3 EQUIVALENT CIRCUIT
The induction motor can be treated essentially as a transformer for analysis. The induction motor has stator leakage reactance, stator copper loss elements as series components, and iron loss and magnetising inductance as shunt elements. The rotor circuit likewise has rotor leakage reactance, rotor copper (aluminum) loss and shaft power as series elements.
The transformer in the centre of the equivalent circuit can be eliminated by adjusting the values of the rotor components in accordance with the effective turns ratio of the transformer. From the equivalent circuit and a basic knowledge of the operation of the induction motor, it can be seen that the magnetising current component and the iron loss of the motor are voltage dependant, and not load dependant. Additionally, the full voltage starting current of a particular motor is voltage and speed dependant, but not load dependant.
The magnetizing current varies depending on the design of the motor. For small motors, the magnetising current may be as high as 60%, but for large two pole motors, the magnetising current is more typically 20 - 25%. At the design voltage, the iron is typically near saturation, so the iron loss and magnetising current do not vary linearly with voltage with small increases in voltage resulting in a high increase in magnetising current and iron loss.
2.1.2.4 STARTING CHARACTERISTICS
In order to perform useful work, the induction motor must be started from rest and both the motor and load accelerated up to full speed. Typically, relying on the high slip characteristics of the motor and enabling it to provide the acceleration torque do this.
Induction motors at rest, appear just like a short-circuited transformer, and if connected to the full supply voltage, draw a very high current known as the "Locked Rotor Current". They also produce torque, which is known as the "Locked Rotor Torque". The Locked Rotor Torque (LRT) and the Locked Rotor Current (LRC) are a function of the terminal voltage to the motor, and the motor design. As the motor accelerates, both the torque and the current will tend to alter with rotor speed if the voltage is maintained constant.
The starting current of a motor, with a fixed voltage, will drop very slowly as the motor accelerates and will only begin to fall significantly when the motor has reached at least 80% full speed. The actual curves for induction motors can vary considerably between designs, but the general trend is for a high current until the motor has almost reached full speed. The LRC of a motor can range from 500% Full Load Current (FLC) to as high as 1400% FLC. Typically, good motors fall in the range of 550% to 750% FLC.
The starting torque of an induction motor starting with a fixed voltage, will drop a little to the minimum torque known as the pull up torque as the motor accelerates, and then rise to a maximum torque known as the breakdown or pull out torque at almost full speed and then drop to zero at synchronous speed. The curve of start torque against rotor speed is dependant on the terminal voltage and the motor/rotor design.
The LRT of an induction motor can vary from as low as 60% Full Load Torque (FLT) to as high as 350% FLT. The pull-up torque can be as low as 40% FLT and the breakdown torque can be as high as 350% FLT. Typical LRTs for medium to large motors are in the order of 120% FLT to 280% FLT.
The power factor of the motor at start is typically 0.1 - 0.25, rising to a maximum as the motor accelerates, and then falling again as the motor approaches full speed.
A motor, which exhibits a high starting current, i.e. 850%, will generally produce a low starting torque, whereas a motor, which exhibits a low starting current, will usually produce a high starting torque. This is the reverse of what is generally expected. The induction motor operates due to the torque developed by the interaction of the stator field and the rotor field. Both of these fields are due to currents which have resistive or in phase components and reactive or out of phase components. The torque developed is dependant on the interaction of the in phase components and consequently is related to the I2R of the rotor. A low rotor resistance will result in the current being controlled by the inductive component of the circuit, yielding a high out of phase current and a low torque. Figures for the locked rotor current and locked rotor torque are almost always quoted in motor data, and certainly are readily available for induction motors. Some manufactures have been known to include this information on the motor nameplate. One additional parameter, which would be of tremendous use in data sheets for those who are engineering motor, starting applications, is the starting efficiency of the motor.
By the starting efficiency of the motor, I refer to the ability of the motor to convert amps into Newton meters. This is a concept not generally recognized within the trade, but one, which is extremely useful when comparing induction motors. The easiest means of developing a meaningful figure of merit is to take the locked rotor torque of the motor (as a percentage of the full load torque) and divide it by the locked rotor current of the motor (as a percentage of the full Load current).
I.e.
Starting efficiency = | Locked Rotor Torque Locked rotor current |
| |
If the terminal voltage to the motor is reduced while it is starting, the current drawn by the motor will be reduced proportionally. The torque developed by the motor is proportional to the current squared, and so a reduction in starting voltage will result in a reduction in starting current and a greater reduction in starting torque. If the start voltage applied to a motor is halved, the start torque will be a quarter; likewise a start voltage of one third will result in a start torque of one ninth.
2.1.2.5 RUNNING CHARACTERISTICS
Once the motor is up to speed, it operates at low slip, at a speed determined by the number of stator poles. The frequency of the current flowing in the rotor is very low. Typically, the full load slip for a standard cage induction motor is less than 5%. The actual full load slip of a particular motor is dependant on the motor design with typical full load speeds of four pole induction motor varying between 1420 and 1480 RPM at 50 Hz. The synchronous speed of a four-pole machine at 50 Hz is 1500 RPM and at 60 Hz a four-pole machine has a synchronous speed of 1800 RPM
The induction motor draws a magnetising current while it is operating. The magnetising current is independent of the load on the machine, but is dependant on the design of the stator and the stator voltage. The actual magnetising current of an induction motor can vary from as low as 20% FLC for large two pole machines to as high as 60% for small eight pole machines. The tendency is for large machines and high-speed machines to exhibit a low magnetising current, while low speed machines and small machines exhibit a high magnetising current. A typical medium sized four pole machine has a magnetizing current of about 33% FLC.
A low magnetizing current indicates a low iron loss, while a high magnetising current indicates an increase in iron loss and a resultant reduction in operating efficiency.
The resistive component of the current drawn by the motor while operating, changes with load, being primarily load current with a small current for losses. If the motor is operated at minimum load, i.e. open shaft, the current drawn by the motor is primarily magnetising current and is almost purely inductive. Being an inductive current, the power factor is very low, typically as low as 0.1. As the shaft load on the motor is increased, the resistive component of the current begins to rise. The average current will noticeably begin to rise when the load current approaches the magnetising current in magnitude. As the load current increases, the magnetising current remains the same and so the power factor of the motor will improve. The full load power factor of an induction motor can vary from 0.5 for a small low speed motorupto0.9 for a large high-speed machine.
The losses of an induction motor comprise: iron loss, copper loss, windage loss and frictional loss. The iron loss, windage loss and frictional losses are all essentially loaded independent, but the copper loss is proportional to the square of the stator current. Typically the efficiency of an induction motor is highest at 3/4 loads and varies from less than 60% for small low speed motors to greater than 92% for large high-speed motors. Operating power factor and efficiencies are generally quoted on the motor data sheets.
2.1.2.6 DESIGN CLASSIFICATION
There are a number of design/performance classifications, which are somewhat uniformly accepted by different standards organizations. These design classifications apply particularly to the rotor design and hence affect the starting characteristics of the motors. The two major classifications of relevance her are design A and design B. Design A motors have a shallow bar rotor, and are characterized by a very high starting current and a low starting torque. Typical values are 850% current and 120% torque. Shallow bar motors usually have a low slip, i.e.1480RPM.
Design B motors have a deeper bar rotor and are characterized by medium start current and medium starting torque. Typical design B values are 650% current and 180% torque. The slip exhibited by design B motors is usually greater than the equivalent design A motors. i.e. 1440 RPM.
Design F motors are often known as Fan motors having a high rotor resistance and high slip characteristics. The high rotor resistance enables the fan motor to be used in a variable speed application where reducing the voltage reduces the speed. Design F motors are used primarily in fan control applications with the motor mounted in the airflow. These are often rated as AOM or Air Over Motor machines.
2.1.2.7 FRAME CLASSIFICATION
Induction motors come in two major frame types, these being Totally Enclosed Forced air Cooled (TEFC), and Drip proof. The TEFC motor is totally enclosed in either an aluminum or cast iron frame with cooling fins running longitudinally on the frame. A fan is fitted externally with a cover to blow air along the fins and provide the cooling. These motors are often installed outside in the elements with no additional protection and so are typically designed to IP55 or better.
Drip proof motors use internal cooling with the cooling air drawn through the windings. They are normally vented at both ends with an internal fan. This can lead to more efficient cooling, but requires that the environment is clean and dry to prevent insulation degradation from dust, dirt and moisture. Drip proof motors are typically IP22 or IP23.
2.1.2.8 TEMPERATURE CLASSIFICATION
There are two main temperature classifications applied to induction motors. These being Class B and Class F. The temperature class refers to the maximum allowable temperature rise of the motor windings at a specified maximum coolant temperature.
Class B motors are rated to operate with a maximum coolant temperature of 40 degrees C and a maximum winding temperature rise of 80 degrees C. This leads to a maximum winding temperature of 120 degrees C.
Class F motors are typically rated to operate with a maximum coolant temperature of 40 degrees C and a maximum temperature rise of 100 degrees C resulting in a potential maximum winding temperature of 140 degrees.
Operating at rated load, but reduced cooling temperatures gives an improved safety margin and increased tolerance for operation under an overload condition. If the coolant temperature is elevated above 40 degrees C then the motor must be derated to avoid premature failure. Note: Some Class F motors are designed for a maximum coolant temperature of 60 degrees C, and so there is no derating necessary up to this temperature.
Operating a motor beyond its maximum will not cause an immediate failure, rather a decrease in the life expectancy of that motor. A common rule of thumb applied to insulation degradation, is that for every ten degree C rise in temperature, the expected life span is halved. Note: the power dissipated in the windings is the copper loss which is proportional to the square of the current, so an increase of 10% in the current drawn, will give an increase of 21% in the copper loss, and therefore an increase of 21% in the temperature rise which is 16.8 degrees C for a Class B motor, and 21 degrees C for a Class F motor. This approximates to the life being reduced to a quarter of that expected if the coolant is at 40 degrees C. Likewise operating the motor in an environment of 50 degrees C at rated load will elevate the insulation temperature by 10 degrees C and halve the life expectancy of the motor.
2.1.2.9 POWER FACTOR CORRECTION
Power factor correction is achieved by the addition of capacitors across the supply to neutralize the inductive component of the current. The power factor correction may be applied either as automatic bank correction at the main plant switchboard, or as static correction installed and controlled at each starter in such a fashion that it is only in circuit when the motor is on line.
Automatic bank correction consists of a number of banks of power factor correction capacitors, each controlled by a contactor, which in turn is controlled by a power factor controller. The power factor controller monitors the supply coming into the switchboard and adds sufficient capacitance to neutralize the inductive current. These controllers are usually set to adjust the power factor to 0.9 - 0.95 lagging. (Inductive)
A contactor when the motor is started and when the motor is stopped control static correction. In the case of a Direct On Line starter, the capacitors are often controlled by the main DOL contactor, which is also controlling the motor. With static correction, it is important that the motor is under corrected rather than over corrected. This is because the capacitance and the inductance of the motor form a resonant circuit. While the motor is connected to the supply, there is no problem. Once the motor is disconnected from the supply, it begins to decelerate. As it decelerates, it generates voltage at the frequency at which it is rotating. If the capacitive reactance equals the inductive reactance, i.e. unity power factor, we have resonance. If the motor is critically corrected (pf = 1) or over corrected, then as the motor slows, the voltage it is generating will pass through the resonant frequency set up between the motor and the capacitors. If this happens, major problems can occur. There will be very high voltages developed across the motor terminals and capacitors causing insulation damage, high resonant currents can flow, and transient torque's generated can cause mechanical equipment failure.
The correct method for sizing static correction capacitors is to determine the magnetising current of the motor being corrected, and connect sufficient capacitance to give 80% current neutralization. Charts and formula based on motor size alone can be totally erroneous and should be avoided if possible. There are some power authorities that specify a fixed amount of KVAR per kilowatt, independent of the size or speed. This is a dangerous practice
2.1.3 SINGLE PHASE MOTORS AND THREE-PHASE MOTOR
In order for a motor to develop a rotating torque in one direction, it is important that the magnetic field rotates in one direction only. In the case of the three-phase motor, there is no problem and the field follows the phase sequence. If voltage is applied to a single winding, there are still multiples of two poles, which alternate between North and South at the supply frequency, but there is no set rotation for the vectors. This field can be correctly considered to be two vectors rotating in opposite directions. To establish a direction of rotation for the vector, a second phase must be added. The second phase is applied to a second winding and is derived from the first phase by using the phase shift of a capacitor in a capacitor start motor, or inductance and resistance in an induction start motor. (Sometimes known as a split phase motor.) Small motors use techniques such as a shaded pole to set the direction of rotation of the motor.
2.1.3.1SLIPRINGMOTORS
Slip ring motors or wound rotor motors are a variation on the standard cage induction motors. The slip ring motor has a set of windings on the rotor which are not short circuited, but are terminated to a set of slip rings for connection to external resistors and contactors. The slip ring motor enables the starting characteristics of the motor to be totally controlled and modified to suit the load. A particular high resistance can result in the pull out torque occurring at almost zero speed providing a very high locked rotor torque at a low locked rotor current. As the motor accelerates, the value of the resistance can be reduced altering the start torque curve in a manner such that the maximum torque is gradually moved towards synchronous speed. This results in a very high starting torque from zero speed to full speed at a relatively low starting current.
2.1.3.2 SQUIRREL CAGE ROTORS:
Most common AC motors use the squirrel cage rotor, which will be found in virtually all domestic and light industrial alternating current motors. The squirrel cage takes its name from its shape - a ring at either end of the rotor, with bars connecting the rings running the length of the rotor. It is typically cast aluminum or copper poured between the iron laminates of the rotor, and usually only the end rings will be visible. The vast majority of the rotor currents will flow through the bars rather than the higher-resistance and usually varnished laminates. Very low voltages at very high currents are typical in the bars and end rings; high efficiency motors will often use cast copper in order to reduce the resistance in the rotor.
In operation, the squirrel cage motor may be viewed as a transformer with a rotating secondary - when the rotor is not rotating in sync with the magnetic field, large rotor currents are induced; the large rotor currents magnetize the rotor and interact with the stator's magnetic fields to bring the rotor into synchronization with the stator's field. An unloaded squirrel cage motor at synchronous speed will consume electrical power only to maintain rotor speed against friction and resistance losses; as the mechanical load increases, so will the electrical load - the electrical load is inherently related to the mechanical load. This is similar to a transformer, where the primary's electrical load is related to the secondary's electrical load.Here we use .5 hp,440v, three phase induction motor for our project.
This is why, as an example, a squirrel cage blower motor may cause the lights in a home to dim as it starts, but doesn't dim the lights when its fanbelt (and therefore mechanical load) is removed. Furthermore, a stalled squirrel cage motor (overloaded or with a jammed shaft) will consume current limited only by circuit resistance as it attempts to start. Unless something else limits the current (or cuts it off completely) overheating and destruction of the winding insulation is the likely outcome.Virtually every washing machine, dishwasher, standalone fan, record player, etc. uses some variant of a squirrel cage motor
2.2 RELAY
A relay is an electrical switch that opens and closes under control of another electrical circuit. In the original form, the switch is operated by an electromagnet to open or close one or many sets of contacts. It was invented by Joseph Henry in 1835. Because a relay is able to control an output circuit of higher power than the input circuit, it can be considered, in a broad sense, to be a form of an electrical amplifier.
2.2.1 OPERATION
When a current flows through the coil, the resulting magnetic field attracts an armature that is mechanically linked to a moving contact. The movement either makes or breaks a connection with a fixed contact. When the current to the coil is switched off, the armature is returned by a force approximately half as strong as the magnetic force to its relaxed position. Usually this is a spring, but gravity is also used commonly in industrial motor starters. Most relays are manufactured to operate quickly. In a low voltage application, this is to reduce noise. In a high voltage or high current application, this is to reduce arcing.
If the coil is energized with DC, a diode is frequently installed across the coil, to dissipate the energy from the collapsing magnetic field at deactivation, which would otherwise generate a spike of voltage and might cause damage to circuit components. If the coil is designed to be energized with AC, a small copper ring can be crimped to the end of the solenoid. This "shading ring" creates a small out-of-phase current, which increases the minimum pull on the armature during the AC cycle.
By analogy with the functions of the original electromagnetic device, a solid-state relay is made with a thyristor or other solid-state switching device. To achieve electrical isolation, a light-emitting diode (LED) is used with a photo transistor.
2.2.2 ELECTROMECHANICAL RELAY
A latching relay has two relaxed states (bistable). These are also called 'keep' relays. When the current is switched off, the relay remains in its last state. This is achieved with a solenoid operating a ratchet and cam mechanism, or by having two opposing coils with an over-center spring or permanent magnet to hold the armature and contacts in position while the coil is relaxed, or with a remnant core. In the ratchet and cam example, the first pulse to the coil turns the relay on and the second pulse turns it off. In the two coil example, a pulse to one coil turns the relay on and a pulse to the opposite coil turns the relay off. This type of relay has the advantage that it consumes power only for an instant, while it is being switched, and it retains its last setting across a power outage.
2.2.3 APPLICATIONS
2.2.3.1 Relays are used:
- To control a high-voltage circuit with a low-voltage signal, as in some types of modems,
- To control a high-current circuit with a low-current signal, as in the starter solenoid of an automobile,
- To detect and isolate faults on transmission and distribution lines by opening and closing circuit breakers (protection relays),
- To isolate the controlling circuit from the controlled circuit when the two are at different potentials, for example when controlling a mains-powered device from a low-voltage switch. The latter is often applied to control office lighting as the low voltage wires are easily installed in partitions, which may be often moved as needs change. They may also be controlled by room occupancy detectors in an effort to conserve energy,
- To perform logic functions. For example, the boolean AND function is realised by connecting NO relay contacts in series, the OR function by connecting NO contacts in parallel. The change-over or Form C contacts perform the XOR (exclusive or) function. Similar functions for NAND and NOR are accomplished using NC contacts. Due to the failure modes of a relay compared with a semiconductor, they are widely used in safety critical logic, such as the control panels of radioactive waste handling machinery.
- To perform time delay functions. Relays can be modified to delay opening or delay closing a set of contacts. A very short (a fraction of a second) delay would use a copper disk between the armature and moving blade assembly. Current flowing in the disk maintains magnetic field for a short time, lengthening release time. For a slightly longer (up to a minute) delay, a dashpot is used. A dashpot is a piston filled with fluid that is allowed to escape slowly. The time period can be varied by increasing or decreasing the flow rate. For longer time periods, a mechanical clockwork timer is installed.
2.2.3.2 RELAY APPLICATION CONSIDERATIONS
A large relay with two coils and many sets of contacts, used in an old telephone switching system.
Selection of an appropriate relay for a particular application requires evaluation of many different factors:
- Number and type of contacts - normally open, normally closed, changeover (double-throw)
- In the case of changeover, there are two types. This style of relay can be manufactured two different ways. "Make before Break" and "Break before Make". The old style telephone switch required Make-before-break so that the connection didn't get dropped while dialing the number. The railroad still uses them to control railroad crossings.
- Rating of contacts - small relays switch a few amperes, large contactors are rated for up to 3000 amperes, alternating or direct current
- Voltage rating of contacts - typical control relays rated 300 VAC or 600 VAC, automotive types to 50 VDC, special high-voltage relays to about 15,000 V
- Coil voltage - machine-tool relays usually 24 VAC or 120 VAC, relays for switchgear may have 125 V or 250 VDC coils, "sensitive" relays operate on a few milliamperes
- Package/enclosure - open, touch-safe, double-voltage for isolation between circuits, explosion proof, outdoor, oil-splashresistant
- Mounting - sockets, plug board, rail mount, panel mount, through-panel mount, enclosure for mounting on walls or equipment
- Switching time - where high speed is required
- "Dry" contacts - when switching very low level signals, special contact materials may be needed such as gold-plated contacts
- Contact protection - suppress arcing in very inductive circuits
- Coil protection - suppress the surge voltage produced when switching the coil current
- Isolation between coil circuit and contacts
- Aerospace or radiation-resistant testing, special quality assurance
- Expected mechanical loads due to acceleration - some relays used in aerospace applications are designed to function in shock loads of 50 g or more
- Accessories such as timers, auxiliary contacts, pilot lamps, test buttons
- Regulatory approvals
- Stray magnetic linkage between coils of adjacent relays on a printed circuit board.
2.3 TRANSFORMER
A transformer is an electrical device that transfers energy from one circuit to another by magnetic coupling, without requiring relative motion between its parts. A transformer comprises two or more coupled windings, and, in most cases, a magnetic core to concentrate magnetic flux. A changing voltage applied to one winding creates a time-varying magnetic flux in the core, which induces a voltage in the other windings.
The transformer is one of the simplest of electrical devices, yet transformer designs and materials continue to be improved.
Transformers come in a range of sizes from a thumbnail-sized coupling transformer hidden inside a stage microphone to huge gigawatt units used to interconnect large portions of national power grids. All operate with the same basic principles and with many similarities in their parts.
2.3.1 CURRENT TRANSFORMER
A current transformer is a type of "instrument transformer" that is designed to provide a current in its secondary which is accurately proportional to the current flowing in its primary. This accuracy is directly related to a number of factors including the following:
- burden,
- rating factor,
- load,
- external electromagnetic fields,
- temperature and
- physical CT configuration.
The burden in a CT metering circuit is essentially the amount of impedance (largely resistive) present. Typical burden ratings for CTs are B-0.1, B-0.2, B-0.5, B-1.0, B-2.0 and B-4.0. This means a CT with a burden rating of B-0.2 can tolerate up to 0.2Ω of impedance in the metering circuit before its output current is no longer a fixed ratio to the primary current. Items that contribute to the burden of a current measurement circuit are switch blocks meters and intermediate conductors. The most common source of excess burden in a current measurement circuit is the conductor between the meter and the CT. Oftentimes, substation meters are located significant distances from the meter cabinets and the excessive length of small gauge conductor creates a large resistance. This problem can be solved by using CT with 1 ampere secondaries which will produce less voltage drop between a CT and its metering devices.
Rating factor is a factor by which the nominal full load current of a CT can be multiplied to determine its absolute maximum measurable primary current. Conversely, the minimum primary current a CT can accurately measure is "light load," or 10% of the nominal current(there are, however, special CTs designed to measure accurately currents as small as 2% of the nominal current). The rating factor of a CT is largely dependent upon ambient temperature. Most CTs have rating factors for 35 degrees Celsius and 55 degrees Celsius. A CT usually demonstrates reduced capacity to maintain accuracy with rising ambient temperature. It is important to be mindful of ambient temperatures and resultant rating factors when CTs are installed inside pad-mounted transformers or poorly ventilated mechanical rooms. Recently, manufacturers have been moving towards lower nominal primary currents with greater rating factors. This is made possible by the development of more efficient ferrites and their corresponding hysteresis curves. This is a distinct advantage over previous CTs because it increases their range of accuracy. For example, a 200:5 CT with a rating factor of 4.0 is most accurate between 20A (light load)and 800A (4.0 times the nominal rating, or "full load," of the CT) of primary current. While previous revisions of CTs were on the order of 500:5 with a rating factor of 1.5 yielding an effective range of 50A to 750A. This is an 11% increase in effective range for two CTs that would be used at similar services. Not to mention, the relative cost of a 500:5 CT is significantly greater than that of a 200:5.
Physical CT configuration is another important factor in reliable CT accuracy. While all electrical engineers are quite comfortable with Gauss' Law, there are some issues when attempting to apply theory to the real world. When conductors passing through a CT are not centered in the circular (or oval) void, slight inaccuracies may occur. It is important to center primary conductors as they pass through CTs to promote the greatest level of CT accuracy. Afterall, in an electric metering circuit, the most inaccurate component is the CT.
Current transformers (CTs) are commonly used in metering and protective relaying in the electrical power industry where they facilitate the safe measurement of large currents, often in the presence of high voltages. The current transformer safely isolates measurement and control circuitry from the high voltages typically present on the circuit being measured.
Current transformers are often constructed by passing a single primary turn (either an insulated cable or an uninsulated bus bar) through a well-insulated toroidal core wrapped with many turns of wire. Current transformers are used extensively for measuring current and monitoring the operation of the power grid. The CT is typically described by its current ratio from primary to secondary. Common secondaries are 1 or 5 amperes. For example, a 4000:5 CT would provide an output current of 5 amperes when the primary was passing 4000 amperes. The secondary winding can be single ratio or multi ratio, with five taps being common for multi ratio CTs. Typically, the secondary connection points are labelled as 1s1, 1s2, 2s1, 2s2 and so on. The multi ratio CTs are typically used for current matching in current differential protective relaying applications. Often, multiple CTs will be installed as a "stack" for various uses (for example, protection devices and revenue metering may use separate CTs). For a three-stacked CT application, the secondary winding connection points are typically labelled Xn, Yn, Zn. Care must be taken that the secondary of a current transformer is not disconnected from its load while current is flowing in the primary, as this will produce a dangerously high voltage across the open secondary and may permanently affect the accuracy of the transformer.
Specially constructed wideband current transformers are also used (usually with an oscilloscope) to measure waveforms of high frequency or pulsed currents within pulsed power systems. One type of specially constructed wideband transformer provides a voltage output that is proportional to the measured current. Another type (called a Rogowski coil) requires an external integrator in order to provide a voltage output that is proportional to the measured current. Unlike CTs used for power circuitry, wideband CTs are rated in output volts per ampere of primary current.
2.3.2 VOLTAGE TRANSFORMERS
Voltage transformers (VTs) or potential transformers (PTs) are another type of instrument transformer, used for metering and protection in high-voltage circuits. They are designed to present negligible load to the supply being measured and to have a precise voltage ratio to accurately step down high voltages so that metering and protective relay equipment can be operated at a lower potential. Typically the secondary of a voltage transformer is rated for 69 or 120 Volts at rated primary voltage, to match the input ratings of protection relays.
The transformer winding high-voltage connection points are typically labelled as H1, H2 (sometimes H0 if it is internally grounded) and X1, X2, and sometimes an X3 tap may be present. Sometimes a second isolated winding (Y1, Y2, Y3) may also be available on the same voltage transformer. The high side (primary) may be connected phase to ground or phase to phase. The low side (secondary) is usually phase to ground.
The terminal identifications (H1, X1, Y1, etc.) are often referred to as polarity. This applies to current transformers as well. At any instant terminals with the same suffix numeral have the same polarity and phase. Correct identification of terminals and wiring is essential for proper operation of metering and protection relays.
While VTs were formerly used for all voltages greater than 240V primary, modern meters eliminate the need VTs for most secondary service voltages. For new, or rework, meter packages, VTs are typically only installed in primary voltage (typically 12.5kV) or generation voltage (13.2kV) meter packages.
2.4 PIC 16F877 Microcontoller
This powerful yet easy to program CMOS FLASH-based 8-bit microcontoller packs Microchip's powerful PIC RISC architecture into a 40-pin package and is upwards compatible with the PIC16C5X, PIC12CXXX and PIC16C7X devices. The PIC16F877 features 256 bytes of EEPROM data memory, self-programming, ICD/ICSP capability, 8 channels of 10-bit Analog-to-Digital (A/D) converter, 3 timers, integrated watchdog, 2 capture/compare/PWM functions, and a synchronous serial port. The synchronous serial port can be configured as either a 3-wire Serial Peripheral Interface (SPI™), 2-wire Inter-Integrated Circuit (I2C™) bus, or a Universal Asynchronous Receiver Transmitter (USART). All of these features make it ideal for more advanced level A/D applications in automotive, industrial, appliances and consumer applications. Since the PIC16F877 is so feature rich, it is often used to develop projects that will not ultimately use the 16F877 but a different member of the mid-range family.
2.4.1 MEMORY ORGANIZATION
There are three memory blocks in each of these PICmicro MCUs. The Program Memory and Data Memory have separate buses so that concurrent access can occur.
PROGRAM MEMORY ORGANIZATION
The PIC16F87X devices have a 13-bit program counter capable of addressing an 8K x 14 program memory space. The PIC16F877/876 devices have 8K x 14 words of FLASH program memory. Accessing a location above the physically implemented address will cause a wraparound. The reset vector is at 0000h and the interrupt vector is at 0004h.
DATA MEMORY ORGANIZATION
The data memory is partitioned into multiple banks, which contain the General Purpose Registers and the Special Function Registers. Bits RP1 (STATUS<6>) and RP0 (STATUS<5>) are the bank select bits. Each bank extends up to 7Fh (128 bytes). The lower locations of each bank are reserved for the Special Function Registers. Above the Special Function Registers are General Purpose Registers, implemented as static RAM. All implemented banks contain Special Function Registers. Some “high use” Special Function Registers from one bank may be mirrored in another bank for code reduction and quicker access.
GENERAL PURPOSE REGISTER FILE
The register file can be accessed either directly, or indirectly through the File Select Register FSR.
SPECIAL FUNCTION REGISTERS
The Special Function Registers are registers used by the CPU and peripheral modules for controlling the desired operation of the device. These registers are implemented as static RAM. The Special Function Registers can be classified into two sets; core (CPU) and peripheral.
STATUS REGISTER
The STATUS register contains the arithmetic status of the ALU, the RESET status and the bank select bits for data memory. Bits RP1 (STATUS<6>) and RP0 (STATUS<5>) are the bank select bits.
2.4.2 I/O PORTS
PIC16F877 has 5 PORTS, named PORTA through PORTE. All are bi-directional ports. Each ports are having corresponding data direction registers i.e. TRISA for PORTA etc. Setting a TRISx bit (=1) will make the corresponding PORT pin an input (i.e., put the corresponding output driver in a hi-impedance mode). Clearing a TRISx bit (=0) will make the corresponding PORTx pin an output (i.e., put the contents of the output latch on the selected pin). Reading the PORTx register reads the status of the pins, whereas writing to it will write to the port latch. All write operations are read-modify-write operations.
Therefore, a write to a port implies that the port pins are read; the value is modified and then written to the port data latch. Port Pins are multiplexed with peripherals Eg.PORTA pins are multiplexed with analog inputs and analog VREF input. All PORT pins have TTL input levels and full CMOS output drivers. PORTA and PORTE requires additional register configuration to select the ports as ANALOG or DIGITAL. The operation of each pin is selected by clearing/setting the control bits in the ADCON1 register (A/D Control Register1).
SPECIAL FEATURES OF THE CPU
These devices have a host of features intended to maximize system reliability, minimize cost through elimination of external components, provide power saving operating modes and offer code protection. These are:
• OSC Selection
• Reset
- Power-on Reset (POR)
- Power-up Timer (PWRT)
- Oscillator Start-up Timer (OST)
- Brownout Reset (BOR)
• Interrupts
• Watchdog Timer (WDT)
• SLEEP
• Code protection
• ID locations
• In-Circuit Serial Programming
• Low Voltage In-Circuit Serial Programming
• In-Circuit Debugger
These devices have a watchdog timer, which can be shut off only through configuration bits. It runs off its own RC oscillator for added reliability. There are two timers that offer necessary delays on power-up. One is the Oscillator Start-up Timer (OST), intended to keep the chip in reset until the crystal oscillator is stable. The other is the Power-up Timer (PWRT), which provides a fixed delay of 72 ms (nominal) on power-up only. It is designed to keep the part in reset while the power supply stabilizes. With these two timers on-chip, most applications need no external reset circuitry. SLEEP mode is designed to offer a very low current power-down mode.
The user can wake-up from SLEEP through external reset, Watchdog Timer Wake-up, or through an interrupt. Several oscillator options are also made available to allow the part to fit the application. The RC oscillator option saves system cost while the LP crystal option saves power. A set of configuration bits is used to select various options.
CONFIGURATION BITS
The configuration bits can be programmed (read as '0') or left unprogrammed (read as '1') to select various device configurations. These bits are mapped in program memory location 2007h. The user will note that address 2007h is beyond the user program memory space. In fact, it belongs to the special test/configuration memory space (2000h - 3FFFh), which can be accessed only during programming.
2.4.3 OSCILLATOR CONFIGURATIONS
OSCILLATOR TYPES:
The PIC16F877 can be operated in four different oscillator modes. The user can program two configuration bits (FOSC1 and FOSC0) to select one of these four modes:
• LP Low Power Crystal
• XT Crystal/Resonator
• HS High Speed Crystal/Resonator
• RC Resistor/Capacitor
CRYSTAL OSCILLATOR/CERAMIC RESONATORS:
In XT, LP or HS modes, a crystal or ceramic resonator is connected to the OSC1/CLKIN and OSC2/CLKOUT pins PIC16F877 oscillator design requires the use of a parallel cut crystal. Use of a series cut crystal may give a frequency out of the crystal manufacturer’s specifications. When in XT, LP or HS modes, the device can have an external clock source to drive the OSC1/CLKIN pin
RESET:
The PIC16F87X differentiates between various kinds of reset:
• Power-on Reset (POR)
• MCLR reset during normal operation
• MCLR reset during SLEEP
• WDT Reset (during normal operation)
• WDT Wake-up (during SLEEP)
• Brown-out Reset (BOR)
Some registers are not affected in any reset condition. Their status is unknown on POR and unchanged in any other reset. Most other registers are reset to a “reset state” on Power-on Reset (POR), on the MCLR and WDT Reset, on MCLR reset during SLEEP, and Brownout Reset (BOR). They are not affected by a WDT Wake-up, which is viewed as the resumption of normal operation. The TO and PD bits are set or cleared differently in different reset situations It should be noted that a WDT Reset does not drive MCLR pin low.
POWER-ON RESET (POR)
A Power-on Reset pulse is generated on-chip when VDD rise is detected (in the range of 1.2V - 1.7V). To take advantage of the POR, tie the MCLR pin directly (or through a resistor) to VDD. This will eliminate external RC components usually needed to create a Power on Reset When the device starts normal operation (exits the reset condition), device operating parameters (voltage, frequency, temperature,...) must be met to ensure operation. If these conditions are not met, the device must be held in reset until the operating conditions are met. Brownout Reset may be used to meet the start-up conditions.
POWER-UP TIMER (PWRT)
The Power-up Timer provides a fixed 72 ms nominal time-out on power-up only from the POR. The Power up Timer operates on an internal RC oscillator. The chip is kept in reset as long as the PWRT is active. The PWRT’s time delay allows VDD to rise to an acceptable level. A configuration bit is provided to enable/disable the PWRT. The power-up time delay will vary from chip to chip due to VDD, temperature and process variation.
OSCILLATOR START-UP TIMER (OST)
The Oscillator Start-up Timer (OST) provides 1024 oscillator cycle (from OSC1 input) delay after the PWRT delay is over. This ensures that the crystal oscillator or resonator has started and stabilized. The OST time-out is invoked only for XT, LP and HS modes and only on Power-on Reset or wake-up from SLEEP.
BROWNOUT RESET (BOR)
The configuration bit, BODEN, can enable or disable the Brown-out Reset circuit. If VDD falls below VBOR (parameter D005, about 4V) for longer than TBOR (parameter #35, about 100 micro Sec), the brownout situation will reset the device. If VDD falls below VBOR for less than TBOR, a reset may not occur. Once the brownout occurs, the device will remain in brownout reset until VDD rises above VBOR. The power-up timer then keeps the device in reset for TPWRT (parameter #33, about 72mS). If VDD should fall below VBOR during TPWRT, the brownout-reset process will restart when VDD rises above VBOR with the power-up timer reset. The power-up timer is always enabled when the brownout reset circuit is enabled regardless of the state of the PWRT configuration bit.
TIME-OUT SEQUENCE
On power-up, the time-out sequence is as follows: The PWRT delay starts (if enabled) when a POR reset occurs. Then OST starts counting 1024 oscillator cycles when PWRT ends (LP, XT, HS). When the OST ends, the device comes out of RESET. If MCLR is kept low long enough, the time-outs will expire. Bringing MCLR high will begin execution immediately. This is useful for testing purposes or to synchronize more than one PIC16F877 device operating in parallel.
TIME-OUT IN VARIOUS SITUATIONS
2.4.4 INTERRUPTS:
The PIC16F87X family has up to 14 sources of interrupt. The interrupt control register (INTCON) records individual interrupt requests in flag bits. It also has individual and global interrupt enable bits. A global interrupt enable bit, GIE (INTCON<7>) enables (if set) all un-masked interrupts or disables (if cleared) all interrupts. When bit GIE is enabled, and an interrupt’s flag bit and mask bit are set, the interrupt will vector immediately. Individual interrupts can be disabled through their corresponding enable bits in various registers. Individual interrupt bits are set regardless of the status of the GIE bit. The GIE bit is cleared on reset. The “return from interrupt” instruction, RETFIE, exits the interrupt routine, as well as sets the GIE bit, which re-enables interrupts. The RB0/INT pin interrupt, the RB port change interrupt and the TMR0 overflow interrupt flags are contained in the INTCON register. The peripheral interrupt flags are contained in the special function registers, PIR1 and PIR2. The corresponding interrupt enable bits are contained in special function registers, PIE1 and PIE2, and the peripheral interrupt enable bit is contained in special function register INTCON.
When an interrupt is responded to, the GIE bit is cleared to disable any further interrupt, the return address is pushed onto the stack and the PC is loaded with 0004h. Once in the interrupt service routine, the source(s) of the interrupt can be determined by polling the interrupt flag bits. The interrupt flag bit(s) must be cleared in software before re-enabling interrupts to avoid recursive interrupts. For external interrupt events, such as the INT pin or PORTB change interrupt, the interrupt latency will be three or four instruction cycles. The exact latency depends when the interrupt event occurs. The latency is the same for one or two cycle instructions. Individual interrupt flag bits are set regardless of the status of their corresponding mask bit or the GIE bit
IN-CIRCUIT SERIAL PROGRAMMING:
PIC16F87X micro controllers can be serially programmed while in the end application circuit. This is simply done with two lines for clock and data and three other lines for power, ground, and the programming voltage. This allows customers to manufacture boards with unprogrammed devices, and then program the micro controller just before shipping the product. This also allows the most recent firmware or a custom firmware to be programmed. When using ICSP, the part must be supplied 4.5V to 5.5V if a bulk erase will be executed. This includes reprogramming of the code protect both from an on state to off-state. For all other cases of ICSP, the part may be programmed at the normal operating voltages. This means calibration values; unique user IDs or user code can be reprogrammed or added.
INSTRUCTION SET SUMMARY
Each PIC16F877 instruction is a 14-bit word divided into an OPCODE, which specifies the instruction type and one or more operands, which further specify the operation of the instruction. The instruction set is highly orthogonal and is grouped into three basic categories:
• Byte-oriented operations
• Bit-oriented operations
• Literal and control operations
All instructions are executed within one single instruction cycle, unless a conditional test is true or the program counter is changed as a result of an instruction. In this case, the execution takes two instruction cycles with the second cycle executed as a NOP. One instruction cycle consists of four oscillator periods. Thus, for an oscillator frequency of 4 MHz, the normal instruction execution time is 1s. If a conditional test is true or the program counter is changed as a result of an instruction, the instruction execution time is 2s.
For byte-oriented instructions, ’f’ represents a file register designator and ’d’ represents a destination designator. The file register designator specifies which file register is to be used by the instruction. The destination designator specifies where the result of the operation is to be placed. If ’d’ is zero, the result is placed in the W register. If ’d’ is one, the result is placed in the file register specified in the instruction. For bit-oriented instructions, ’b’ represents a bit field designator, which selects the number of the bit affected by the operation, while ’f’ represents the number of the file in which the bit is located. For literal and control operations, ’k’ represents an eight or eleven bit constant or literal value.
2.5 LCD
2.5.1 DESCRIPTION
A liquid crystal display (commonly abbreviated LCD) is a thin, flat display device made up of any number of color or monochrome pixels arrayed in front of a light source or reflector. It is prized by engineers because it uses very small amounts of electric power, and is therefore suitable for use in battery-powered electronic devices.
Each pixel of an LCD consists of a layer of perpendicular molecules aligned between two transparent electrodes, and two polarizing filters, the axes of polarity of which are perpendicular to each other. With no liquid crystal between the polarizing filters, light passing through one filter would be blocked by the electrodes.
The surfaces of the electrodes that are in contact with the liquid crystal material are treated so as to align the liquid crystal molecules in a particular direction. This treatment typically consists of a thin polymer layer that is unidirectionally rubbed using a cloth (the direction of the liquid crystal alignment is defined by the direction of rubbing).
Before applying an electric field, the orientation of the liquid crystal molecules is determined by the alignment at the surfaces. In a twisted nematic device (the most common liquid crystal device), the surface alignment directions at the two electrodes are perpendicular, and so the molecules arrange themselves in a helical structure, or twist. Because the liquid crystal material is birefringent, light passing through one polarizing filter is rotated by the liquid crystal helix as it passes through the liquid crystal layer, allowing it to pass through the second polarized filter. Half of the light is absorbed by the first polarizing filter, but otherwise the entire assembly is transparent.
When a voltage is applied across the electrodes, a torque acts to align the liquid crystal molecules parallel to the electric field, distorting the helical structure (this is resisted by elastic forces since the molecules are constrained at the surfaces). This reduces the rotation of the polarization of the incident light, and the device appears gray. If the applied voltage is large enough, the liquid crystal molecules are completely untwisted and the polarization of the incident light is not rotated at all as it passes through the liquid crystal layer. This light will then be polarized perpendicular to the second filter, and thus be completely blocked and the pixel will appear black. By controlling the voltage applied across the liquid crystal layer in each pixel, light can be allowed to pass through in varying amounts, correspondingly illuminating the pixel.
With a twisted nematic liquid crystal device it is usual to operate the device between crossed polarizers, such that it appears bright with no applied voltage. With this setup, the dark voltage-on state is uniform. The device can be operated between parallel polarizers, in which case the bright and dark states are reversed (in this configuration, the dark state appears blotchy).
Both the liquid crystal material and the alignment layer material contain ionic compounds. If an electric field of one particular polarity is applied for a long period of time, this ionic material is attracted to the surfaces and degrades the device performance. This is avoided by applying either an alternating current, or by reversing the polarity of the electric field as the device is addressed (the response of the liquid crystal layer is identical, regardless of the polarity of the applied field).
When a large number of pixels is required in a display, it is not feasible to drive each directly since then each pixel would require independent electrodes. Instead, the display is multiplexed. In a multiplexed display, electrodes on one side of the display are grouped and wired together (typically in columns), and each group gets its own voltage source. On the other side, the electrodes are also grouped (typically in rows), with each group getting a voltage sink. The groups are designed so each pixel has a unique, unshared combination of source and sink. The electronics, or the software driving the electronics then turns on sinks in sequence, and drives sources for the pixels of each sink.
2.5.2 SPECIFICATIONS OF LCD
Important factors to consider when evaluating an LCD monitor include
- RESOLUTION: unlike CRT monitors, LCD monitors have a native-supported resolution for best display effect.
- DOT PITCH: the granularity of LCD pixels. The smaller, the better.
- VIEWABLE SIZE: The length of diagonal of a LCD panel
- Response time (sync rate)
- Matrix type (passive or active)
- Viewing angle
- COLOR SUPPORT: How many types of colors are supported.
- BRIGHTNESS: The amount of light emitted from the display.
- Contrast ratio
- Aspect ratio: 4 by 3, 16 by 9, 16 by 10, etc.
- Input ports (e.g. DVI, VGA, or even S-Video ).
LCDs with a small number of segments, such as those used in digital watches and pocket calculators, have a single electrical contact for each segment. An external dedicated circuit supplies an electric charge to control each segment. This display structure is unwieldy for more than a few display elements.
Small monochrome displays such as those found in personal organizers, or older laptop screens have a passive-matrix structure employing super-twisted nematic (STN) or double-layer STN (DSTN) technology (DSTN corrects a color-shifting problem with STN). Each row or column of the display has a single electrical circuit. The pixels are addressed one at a time by row and column addresses. This type of display is called a passive matrix because the pixel must retain its state between refreshes without the benefit of a steady electrical charge. As the number of pixels (and, correspondingly, columns and rows) increases, this type of display becomes less feasible. Very slow response times and poor contrast are typical of passive-matrix LCDs. High-resolution color displays such as modern LCD computer monitors and televisions use an active matrix structure. A matrix of thin-film transistors (TFTs) is added to the polarizing and color filters. Each pixel has its own dedicated transistor, allowing each column line to access one pixel. When a row line is activated, all of the column lines are connected to a row of pixels and the correct voltage is driven onto all of the column lines. The row line is then deactivated and the next row line is activated. All of the row lines are activated in sequence during a refresh operation. Active-matrix displays are much brighter and sharper than passive-matrix displays of the same size, and generally have quicker response times, producing much better images.
2.5.3 PASSIVE AND ACTIVE MATRIX
Passive-matrix LCDs use a simple grid to supply the charge to a particular pixel on the display. Creating the grid is quite a process! It starts with two glass layers called substrates. One substrate is given columns and the other is given rows made from a transparent conductive material.
This is usually indium-tin oxide. The rows or columns are connected to integrated circuits that control when a charge is sent down a particular column or row. The liquid crystal material is sandwiched between the two glass substrates, and a polarizing film is added to the outer side of each substrate. To turn on a pixel, the integrated circuit sends a charge down the correct column of one substrate and a ground activated on the correct row of the other. The row and column intersect at the designated pixel, and that delivers the voltage to untwist the liquid crystals at that pixel.
The simplicity of the passive-matrix system is beautiful, but it has significant drawbacks, notably slow response time and imprecise voltage control. Response time refers to the LCD's ability to refresh the image displayed. The easiest way to observe slow response time in a passive-matrix LCD is to move the mouse pointer quickly from one side of the screen to the other. You will notice a series of "ghosts" following the pointer. Imprecise voltage control hinders the passive matrix's ability to influence only one pixel at a time. When voltage is applied to untwist one pixel, the pixels around it also partially untwist, which makes images appear fuzzy and lacking in contrast.
Active-matrix LCDs depend on thin film transistors (TFT). Basically, TFTs are tiny switching transistors and capacitors. They are arranged in a matrix on a glass substrate. To address a particular pixel, the proper row is switched on, and then a charge is sent down the correct column. Since all of the other rows that the column intersects are turned off, only the capacitor at the designated pixel receives a charge. The capacitor is able to hold the charge until the next refresh cycle. And if we carefully control the amount of voltage supplied to a crystal, we can make it untwist only enough to allow some light through.
3. TYPES OF FAULTS
Ø OVER VOLTAGE
Ø UNDER VOLTAGE
Ø UNBALANCED VOLTAGE
Ø SINGLE PHASING
Ø BLOCKED ROTOR
Ø OVER LOAD
3.1 OVER VOLTAGE FAULT
Over Voltage will cause the motor to be over fluxed. This will cause a rapid increase in magnetizing current, iron loss and a build up of heat in the motor. Over voltage will cause a reduction in the work current drawn by the motor. The simulation output for the over voltage fault is shown in the figure 3.1 in which over voltage fault is introduced at 5.5ms. The change in characteristics was identified.
3.2 SINGLE PHASING
The abnormal condition that experienced by motor is failure of phase there by load is concentrated other phase that leads to overloading on that particular phase. This will damage the insulation and eventually the motor will be degraded. A 3Ø induction motor continues to run even if one of supply lines is disconnected. The whole power is then supplied by other two phases and those windings are likely to overheat. In case of large motors, even small change in current damage of motor winding due to overloading .If motor starts due to phase loss, severe damage to rotor is possible while starting. Single phasing is extreme unbalanced conditions for 3Ø motor. In this condition healthy phase increases by √3 times. Thus due to increased current, temperature rises and motor is damaged. The simulation output for the single phasing fault is shown in the figure 3.2 in which single phasing fault is introduced at 5.5ms. The change in characteristics was identified
3.3 BLOCKED ROTOR
Locked rotor conditions are a similar to overloading. It is an extreme case of overloading. This condition occurs when the load on rotor is very heavy such that the rotor is not capable of turning (i.e.) Motor capacity is less. In at start, rotor does not rotate itself. In this situation, the line current increases to 4 or 5 times the rated current. If the motor is allowed turn continuously at this state, motor burn out will occur quickly depending on the insulation class. The simulation output for the blocked rotor fault is shown in the figure 3.3 in which blocked rotor fault is introduced at 5.5ms. The change in characteristics was identified.
3.4 UNDER VOLTAGE FAULT
Under voltage will reduce the flux in the motor. This will reduce the magnetizing current and the maximum torque capacity of the motor. Under voltage will cause the work component of the current drawn by the motor to be increased. Under voltage will increase the running slip of the motor. The simulation output for the under voltage fault is shown in the figure 3.4 in which under voltage fault is introduced at 5.5ms. The change in characteristics was identified.
3.5 OVERLOAD FAULT
Thermal over load relay offer good protection against short,medium & long duration overloads but may not provide protection against heavy over loads. The long time induction over current relays provide good protection against heavy over loads but over protection against light and medium overloads.due to overload fault increase the heating of stator and rotor windings due intake of large amount of current .the simulation output of overload fault is given below .in this speed fall below negative and maximum current exist for large period of time .therefore this fault has to be detected at right period of time and to avoid the damage of windings. The simulation output for the overload fault is shown in the figure 3.5 in which overload fault is introduced at 5.5ms. The change in characteristics was identified.
3.6 UNBALANCED VOLTAGE
Large induction motors are sensitive to unbalances in supply voltage. The negative sequence components which comes into picture because of the unbalance in the supply, is particular troublesome this because the motor offers very small impedance to the negative sequence currents. In fact the negative sequence is less than the positive sequence stand still impedance. Thus, 4% negative sequence supply voltage causes more than 24% negative sequence current to be drawn by the motor, if the starting current of the motor is six times the full load current is cause the increased heating of the stator further the magnetic field due to negative sequence rotates at synchronous speed (Ns) in a direction opposite to that of the rotor which is rotating at the speed equal to (sNs) which is slightly less than the synchronous speed, where s is the slip of the motor. This causes currents of f (2-s) frequency therefore double the frequency is to be induced in the rotor circuit.
5. RECTIFIERS AND REGULATING CKT
The fault is detected by using micro controller circuit the input to the micro controller circuit is taken from the ct &pt output before it is fed to the micro controller it is to be rectified and regulated to particular value for which the microcontoller operate. Therefore the rectifier and regulating circuit for above necessary operation is design by using orcade /pspice software in which the input is either output from pt or c.t. But the ct output is converted to voltage by using the resistance connected across it. Then the a.c voltage is converted to dc by rectifier circuit and using the capacitor filters the output and pot circuit regulates the output and the output dc voltage is filtered and the corresponding output is fed to micro controller circuit.
6. FUZZY LOGIC
The concept of Fuzzy Logic (FL) was conceived by Lotfi Zadeh, a professor at the University of California at Berkley, and presented not as a control methodology, but as a way of processing data by allowing partial set membership rather than crisp set membership or non-membership
6.1 DE
In this context, FL is a problem-solving control system methodology that lends itself to implementation in systems ranging from simple, small, embedded micro-controllers to large, networked, multi-channel PC or workstation-based data acquisition and control systems. It can be implemented in hardware, software, or a combination of both. FL provides a simple way to arrive at a definite conclusion based upon vague, ambiguous, imprecise, noisy, or missing input information. FL's approach to control problems mimics how a person would make decisions, only much faster.
6.2 A simple fuzzy logic control system has the following features:
1. Fixed and uniform input–and output scaling factors.
2. Flat, single-partition rule-base with fixed and non-interactive rules. All the rules have the same degree of certainty and confidence ‘ equal to unity.
3. Fixed membership functions.
4. Limited number of rule, which increase exponentially which the number of input variables.
5. Fixed meta knowledge including the methodology for approximate reasoning, rules aggregation, and output defuzzification.
6. Low-level control and no hierarchical rule structure.
7. CONCLUSION
This paper studied the use of fuzzy logic based fault diagnostics of induction motors. The idea was to use data provided by accurate MATLAB simulations of motor operation under different fault and load conditions to create rule based fuzzy logic model, which can be used for online fault diagnosis. The fuzzy logic models are created for each phase of the three phase induction motor, and each fault condition is handled separately for this work a model of a ½ HP induction motor was simulated for cases of a healthy, and stator fault in motor. Therefore motor was easily diagnose from the fault and made to work normally.
No comments:
Post a Comment
leave your opinion