A continuously variable transmission (CVT) is a transmission that can change steplessly through an infinite number of effective gear ratios between maximum and minimum values. This contrasts with other mechanical transmissions that offer a fixed number of gear ratios. The flexibility of a CVT allows the driving shaft to maintain a constant angular velocity over a range of output velocities. This can provide better fuel economy than other transmissions by enabling the engine to run at its most efficient revolutions per minute (RPM) for a range of vehicle speeds.
Alternatively it can be used to maximize the performance of a vehicle by allowing the engine to turn at the RPM at which it produces peak power. This is typically higher than the RPM that achieves peak efficiency. Finally, a CVT does not strictly require the presence of a clutch, allowing the dismissal thereof. In some vehicles though (ie motorcycles), a centrifugal clutch is nevertheless added , however this is only to provide a "neutral" stance on a motorcycle (useful when idling).
Shifting gears at the right RPM is surely no less than having the precision a Formula One driver has. But, in practical terms, it is not possible for an everyday driver to do the same. So, what if there was a technology that adjusted the gear ratio of the transmission according to the driver’s gear and the speed at which he/she is driving. This would not only avoid high wear and tear of the engine, clutch plates etc. it would also bring up the efficiency of the engine and increase engine life expectancy. Continuously Variable Transmission or CVT is the idea behind keeping engines better for a longer time. Primarily found in automatic transmissions, a CVT plays the role of a smooth gear transition even while the driver has the control of the gears in a paddle shift or tip-tronic mode, the smooth transition is taken care by the CVT. Naturally, when the gear transition is smooth, it also reduces knocking in the engine.
Unlike traditional automatic transmission which have a certain levels at which the gears would shift which locking wheels typically which are in a manual, a CVT has a pully based system in which two pulleys are connected to each other with a chain or a metal pulley. One pulley is connected to the engine and the other, to the drive wheels. This makes the engine decide on its own as to which gear to run the car in. The basic refernce in CVT is given as low gear and high gear since there is no specified ratio which a CVT follows.
he low-gear high-gear theory comes from the drive pulley having a variable diameter which visually looks like tow inverted cones facing each other. The variable diameter is made in such a way that it adjusts according to the input given to the engine by the driver. When the car is in idle or slow position, the distance between the cones is maximum and the belt takes more time to complete the cycle. As the speed is increased, the distance between the cones also decreases and the transition from a low speed to higher speed was smoother. The distance between the cones becomes the least, with space for the movement of the belt, when the engine is at its lowest torque. Mostly, CVTs were earlier used in tractors, snowmobiles etc. The main reliability factor came at the use of rubber belts.
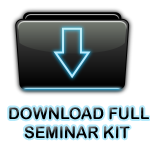
TYPES׃
The V-belt needs to be very stiff in the pulley's axial direction in order to make only short radial movements while sliding in and out of the pulleys. This can be achieved by a chain and not by homogeneous rubber. To dive out of the pulleys one side of the belt must push. This again can be done only with a chain. Each element of the chain has conical sides, which perfectly fit to the pulley if the belt is running on the outermost radius. As the belt moves into the pulleys the contact area gets smaller. The contact area is proportional to the number of elements, thus the chain has lots of very small elements. The shape of the elements is governed by the static of a column. The pulley-radial thickness of the belt is a compromise between maximum gear ratio and torque. For the same reason the axis between the pulleys is as thin as possible. A film of lubricant is applied to the pulleys. It needs to be thick enough so that the pulley and the belt never touch and it must be thin in order not to waste power when each element dives into the lubrication film. Additionally, the chain elements stabilize about 12 steel bands. Each band is thin enough so that it bends easily. If bending, it has a perfect conical surface on its side. In the stack of bands each band corresponds to a slightly different gear ratio, and thus they slide over each other and need oil between them. Also the outer bands slide through the stabilizing chain, while the center band can be used as the chain linkage
2) Toroidal or roller-based CVT (Extroid CVT )
Toroidal CVTs are made up of discs and rollers that transmit power between the discs. The discs can be pictured as two almost conical parts, point to point, with the sides dished such that the two parts could fill the central hole of a torus. One disc is the input, and the other is the output (they do not quite touch). Power is transferred from one side to the other by rollers. When the roller's axis is perpendicular to the axis of the near-conical parts, it contacts the near-conical parts at same-diameter locations and thus gives a 1:1 gear ratio. The roller can be moved along the axis of the near-conical parts, changing angle as needed to maintain contact. This will cause the roller to contact the near-conical parts at varying and distinct diameters, giving a gear ratio of something other than 1:1. Systems may be partial or full toroidal. Full toroidal systems are the most efficient design while partial toroidals may still require a torque converter, and hence lose efficiency.
3) Magnetic CVT
magnetic continuous variable transmission system has been developed at the University of Sheffield in 2006 and is now (2011) commercially available. Two rotating transmission disks, each with magnets attached, synchronously revolve. A change in the radius of the magnets on each of the disks causes a change in the transmission ratio.
The IVT dates back to before the 1930s; the original design converts rotary motion to oscillating motion and back to rotary motion using roller clutches. The stroke of the intermediate oscillations is adjustable, varying the output speed of the shaft. This original design is still manufactured today, and an example and animation of this IVT can be found here. Paul B. Pires created a more compact (radially symmetric) variation that employs a ratchet mechanism instead of roller clutches, so it doesn't have to rely on friction to drive the output. An article and sketch of this variation can be found here
Most IVTs result from the combination of a CVT with a planetary gear system (which is also known as an epicyclic gear system) which enforces an IVT output shaft rotation speed which is equal to the difference between two other speeds within the IVT. This IVT configuration uses its CVT as a continuously variable regulator (CVR) of the rotation speed of any one of the three rotators of the planetary gear system (PGS). If two of the PGS rotator speeds are the input and output of the CVR, there is a setting of the CVR that results in the IVT output speed of zero. The maximum output/input ratio can be chosen from infinite practical possibilities through selection of additional input or output gear, pulley or sprocket sizes without affecting the zero output or the continuity of the whole system. The IVT is always engaged, even during its zero output adjustment.
IVTs can in some implementations offer better efficiency when compared to other CVTs as in the preferred range of operation because most of the power flows through the planetary gear system and not the controlling CVR. Torque transmission capability can also be increased. There's also possibility to stage power splits for further increase in efficiency, torque transmission capability and better maintenance of efficiency over a wide gear ratio range.
An example of a true IVT is the SIMKINETICS SIVAT that uses a ratcheting CVR. Its CVR ratcheting mechanism contributes minimal IVT output ripple across its range of ratios.
Another example of a true IVT is the Hydristor because the front unit connected to the engine can displace from zero to 27 cubic inches per revolution forward and zero to -10 cubic inches per revolution reverse. The rear unit is capable of zero to 75 cubic inches per revolution.
5) Ratcheting CVT
The ratcheting CVT is a transmission that relies on static friction and is based on a set of elements that successively become engaged and then disengaged between the driving system and the driven system, often using oscillating or indexing motion in conjunction with one-way clutches or ratchets that rectify and sum only "forward" motion. The transmission ratio is adjusted by changing linkage geometry within the oscillating elements, so that the summed maximum linkage speed is adjusted, even when the average linkage speed remains constant. Power is transferred from input to output only when the clutch or ratchet is engaged, and therefore when it is locked into a static friction mode where the driving & driven rotating surfaces momentarily rotate together without slippage.
These CVTs can transfer substantial torque, because their static friction actually increases relative to torque throughput, so slippage is impossible in properly designed systems. Efficiency is generally high, because most of the dynamic friction is caused by very slight transitional clutch speed changes. The drawback to ratcheting CVTs is vibration caused by the successive transition in speed required to accelerate the element, which must supplant the previously operating and decelerating, power transmitting element.
Ratcheting CVTs are distinguished from VDPs and roller-based CVTs by being static friction-based devices, as opposed to being dynamic friction-based devices that waste significant energy through slippage of twisting surfaces. An example of a ratcheting CVT is one prototyped as a bicycle transmission protected under U.S. Patent 5,516,132 in which strong pedalling torque causes this mechanism to react against the spring, moving the ring gear/chainwheel assembly toward a concentric, lower gear position. When the pedaling torque relaxes to lower levels, the transmission self-adjusts toward higher gears, accompanied by an increase in transmission vibration.
6) Hydrostatic CVTs
Hydrostatic transmissions use a variable displacement pump and a hydraulic motor. All power is transmitted by hydraulic fluid. These types can generally transmit more torque, but can be sensitive to contamination. Some designs are also very expensive. However, they have the advantage that the hydraulic motor can be mounted directly to the wheel hub, allowing a more flexible suspension system and eliminating efficiency losses from friction in the drive shaft and differential components. This type of transmission is relatively easy to use because all forward and reverse speeds can be accessed using a single lever.
An integrated hydrostatic transaxle (IHT) uses a single housing for both hydraulic elements and gear-reducing elements. This type of transmission, most commonly manufactured by Hydro-Gear[citation needed], has been effectively applied to a variety of inexpensive and expensive versions of ridden lawn mowers and garden tractors. Many versions of riding lawn mowers and garden tractors propelled by a hydrostatic transmission are capable of pulling a reverse tine tiller and even a single bladed plow.
One class of riding lawn mower that has recently gained in popularity with consumers is zero turning radius mowers. These mowers have traditionally been powered with wheel hub mounted hydraulic motors driven by continuously variable pumps, but this design is relatively expensive. Hydro-Gear, created the first cost-effective integrated hydrostatic transaxle suitable for propelling consumer zero turning radius mowers.
Some heavy equipment may also be propelled by a hydrostatic transmission; e.g. agricultural machinery including foragers, combines, and some tractors. A variety of heavy earth-moving equipment manufactured by Caterpillar Inc., e.g. compact and small wheel loaders, track type loaders and tractors, skid-steered loaders and asphalt compactors use hydrostatic transmission. Hydrostatic CVTs are usually not used for extended duration high torque applications due to the heat that is generated by the flowing oil.
The Honda DN-01 motorcycle is the first road-going consumer vehicle with hydrostatic drive that employs a variable displacement axial piston pump with a variable-angle swashplate.
7) Variable toothed wheel transmission
A variable toothed wheel transmission is not a true CVT that can alter its ratio in infinite increments, but rather approaches CVT capability by having a large number of ratios, typically 49. This transmission relies on a toothed wheel positively engaged with a chain where the toothed wheel has the ability to add or subtract a tooth at a time in order to alter its ratio relative to the chain it is driving. The "toothed wheel" can take on many configurations including ladder chains, drive bars and sprocket teeth. The huge advantage of this type of CVT is that it is a positive mechanical drive and thus does not have the frictional losses and limitations of the roller-based or VDP CVT’s. The challenge in this type of CVT is to add or subtract a tooth from the toothed wheel in a very precise and controlled way in order to maintain synchronized engagement with the chain. This type of transmission has the potential to change ratios under load because of the large number of ratios, resulting in the order of 3% ratio change differences between ratios, thus a clutch or torque converter is necessary only for pull-away. No CVTs of this type are in commercial use, probably because of above mentioned development challenge.
8) Single Tooth Cone CVT
A single tooth cone CVT is a non-friction CVT design. Like an iCVT a single tooth cone it also does not depend on friction to transmit torque; however, it does not have the weaknesses an iCVT has.
The details of a Single Tooth Cone CVT can be found below:
9) Cone CVTs
A cone CVT varies the effective gear ratio using one or more conical rollers. The simplest type of cone CVT, the single-cone version, uses a wheel that moves along the slope of the cone, creating the variation between the narrow and wide diameters of the cone.
The more sophisticated twin cone mesh system is also a type of cone CVT.
In a CVT with oscillating cones, the torque is transmitted via friction from a variable number of cones (according to the torque to be transmitted) to a central, barrel-shaped hub. The side surface of the hub is convex with a specific radius of curvature which is smaller than the concavity radius of the cones. In this way, there will be only one (theoretical) contact point between each cone and the hub at any time.
A new CVT using this technology, the Warko, was presented in Berlin during the 6th International CTI Symposium of Innovative Automotive Transmissions, on December 3–7, 2007.
A particular characteristic of the Warko is the absence of a clutch: the engine is always connected to the wheels, and the rear drive is obtained by means of an epicyclic system in output. This system, named “power split”, allows the engine to have a "neutral gear": when the engine turns (connected to the sun gear of the epicyclic system), the variator (i.e., the planetary gears) will compensate for the engine rotation, so the outer ring gear (which provides output) remains stationary.
10) Radial roller CVT
The working principle of this CVT is similar to that of conventional oil compression engines, but, instead of compressing oil, common steel rollers are compressed.
For more details see EP1688645A1
Prototype applications for wind farms
Inside mechanical parts
The motion transmission between rollers and rotors is assisted by an adapted traction fluid, which ensures the proper friction between the surfaces and slows down wearing thereof. Unlike other systems, the radial rollers do not show a tangential speed variation (delta) along the contact lines on the rotors. From this, a greater mechanical efficiency and working life are obtained. The main advantages of this CVT are the manufacturing inexpensiveness and the high power efficiency.
HOW DOES IT WORK?
Alternatively it can be used to maximize the performance of a vehicle by allowing the engine to turn at the RPM at which it produces peak power. This is typically higher than the RPM that achieves peak efficiency. Finally, a CVT does not strictly require the presence of a clutch, allowing the dismissal thereof. In some vehicles though (ie motorcycles), a centrifugal clutch is nevertheless added , however this is only to provide a "neutral" stance on a motorcycle (useful when idling).
Unlike traditional automatic transmission which have a certain levels at which the gears would shift which locking wheels typically which are in a manual, a CVT has a pully based system in which two pulleys are connected to each other with a chain or a metal pulley. One pulley is connected to the engine and the other, to the drive wheels. This makes the engine decide on its own as to which gear to run the car in. The basic refernce in CVT is given as low gear and high gear since there is no specified ratio which a CVT follows.
he low-gear high-gear theory comes from the drive pulley having a variable diameter which visually looks like tow inverted cones facing each other. The variable diameter is made in such a way that it adjusts according to the input given to the engine by the driver. When the car is in idle or slow position, the distance between the cones is maximum and the belt takes more time to complete the cycle. As the speed is increased, the distance between the cones also decreases and the transition from a low speed to higher speed was smoother. The distance between the cones becomes the least, with space for the movement of the belt, when the engine is at its lowest torque. Mostly, CVTs were earlier used in tractors, snowmobiles etc. The main reliability factor came at the use of rubber belts.

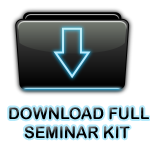
TYPES׃
1) Variable-diameter pulley (VDP) or Reeves drive
In this most common CVT system, there are two V-belt pulleys that are split perpendicular to their axes of rotation, with a V-belt running between them. The gear ratio is changed by moving the two sheaves of one pulley closer together and the two sheaves of the other pulley farther apart. Due to the V-shaped cross section of the belt, this causes the belt to ride higher on one pulley and lower on the other. Doing this changes the effective diameters of the pulleys, which in turn changes the overall gear ratio. The distance between the pulleys does not change, and neither does the length of the belt, so changing the gear ratio means both pulleys must be adjusted (one bigger, the other smaller) simultaneously in order to maintain the proper amount of tension on the belt.The V-belt needs to be very stiff in the pulley's axial direction in order to make only short radial movements while sliding in and out of the pulleys. This can be achieved by a chain and not by homogeneous rubber. To dive out of the pulleys one side of the belt must push. This again can be done only with a chain. Each element of the chain has conical sides, which perfectly fit to the pulley if the belt is running on the outermost radius. As the belt moves into the pulleys the contact area gets smaller. The contact area is proportional to the number of elements, thus the chain has lots of very small elements. The shape of the elements is governed by the static of a column. The pulley-radial thickness of the belt is a compromise between maximum gear ratio and torque. For the same reason the axis between the pulleys is as thin as possible. A film of lubricant is applied to the pulleys. It needs to be thick enough so that the pulley and the belt never touch and it must be thin in order not to waste power when each element dives into the lubrication film. Additionally, the chain elements stabilize about 12 steel bands. Each band is thin enough so that it bends easily. If bending, it has a perfect conical surface on its side. In the stack of bands each band corresponds to a slightly different gear ratio, and thus they slide over each other and need oil between them. Also the outer bands slide through the stabilizing chain, while the center band can be used as the chain linkage
2) Toroidal or roller-based CVT (Extroid CVT )
Toroidal CVTs are made up of discs and rollers that transmit power between the discs. The discs can be pictured as two almost conical parts, point to point, with the sides dished such that the two parts could fill the central hole of a torus. One disc is the input, and the other is the output (they do not quite touch). Power is transferred from one side to the other by rollers. When the roller's axis is perpendicular to the axis of the near-conical parts, it contacts the near-conical parts at same-diameter locations and thus gives a 1:1 gear ratio. The roller can be moved along the axis of the near-conical parts, changing angle as needed to maintain contact. This will cause the roller to contact the near-conical parts at varying and distinct diameters, giving a gear ratio of something other than 1:1. Systems may be partial or full toroidal. Full toroidal systems are the most efficient design while partial toroidals may still require a torque converter, and hence lose efficiency.
3) Magnetic CVT
magnetic continuous variable transmission system has been developed at the University of Sheffield in 2006 and is now (2011) commercially available. Two rotating transmission disks, each with magnets attached, synchronously revolve. A change in the radius of the magnets on each of the disks causes a change in the transmission ratio.
4) Infinitely Variable Transmission (IVT)
A specific type of CVT is the infinitely variable transmission (IVT), in which the range of ratios of output shaft speed to input shaft speed includes a zero ratio that can be continuously approached from a defined "higher" ratio. A zero output speed (low gear) with a finite input speed implies an infinite input-to-output speed ratio, which can be continuously approached from a given finite input value with an IVT. Low gears are a reference to low ratios of output speed to input speed. This low ratio is taken to the extreme with IVTs, resulting in a "neutral", or non-driving "low" gear limit, in which the output speed is zero. Unlike neutral in a normal automotive transmission, IVT output rotation may be prevented because the backdriving (reverse IVT operation) ratio may be infinite, resulting in impossibly high backdriving torque; ratcheting IVT output may freely rotate forward, though.The IVT dates back to before the 1930s; the original design converts rotary motion to oscillating motion and back to rotary motion using roller clutches. The stroke of the intermediate oscillations is adjustable, varying the output speed of the shaft. This original design is still manufactured today, and an example and animation of this IVT can be found here. Paul B. Pires created a more compact (radially symmetric) variation that employs a ratchet mechanism instead of roller clutches, so it doesn't have to rely on friction to drive the output. An article and sketch of this variation can be found here
Most IVTs result from the combination of a CVT with a planetary gear system (which is also known as an epicyclic gear system) which enforces an IVT output shaft rotation speed which is equal to the difference between two other speeds within the IVT. This IVT configuration uses its CVT as a continuously variable regulator (CVR) of the rotation speed of any one of the three rotators of the planetary gear system (PGS). If two of the PGS rotator speeds are the input and output of the CVR, there is a setting of the CVR that results in the IVT output speed of zero. The maximum output/input ratio can be chosen from infinite practical possibilities through selection of additional input or output gear, pulley or sprocket sizes without affecting the zero output or the continuity of the whole system. The IVT is always engaged, even during its zero output adjustment.
IVTs can in some implementations offer better efficiency when compared to other CVTs as in the preferred range of operation because most of the power flows through the planetary gear system and not the controlling CVR. Torque transmission capability can also be increased. There's also possibility to stage power splits for further increase in efficiency, torque transmission capability and better maintenance of efficiency over a wide gear ratio range.
An example of a true IVT is the SIMKINETICS SIVAT that uses a ratcheting CVR. Its CVR ratcheting mechanism contributes minimal IVT output ripple across its range of ratios.
Another example of a true IVT is the Hydristor because the front unit connected to the engine can displace from zero to 27 cubic inches per revolution forward and zero to -10 cubic inches per revolution reverse. The rear unit is capable of zero to 75 cubic inches per revolution.
5) Ratcheting CVT
The ratcheting CVT is a transmission that relies on static friction and is based on a set of elements that successively become engaged and then disengaged between the driving system and the driven system, often using oscillating or indexing motion in conjunction with one-way clutches or ratchets that rectify and sum only "forward" motion. The transmission ratio is adjusted by changing linkage geometry within the oscillating elements, so that the summed maximum linkage speed is adjusted, even when the average linkage speed remains constant. Power is transferred from input to output only when the clutch or ratchet is engaged, and therefore when it is locked into a static friction mode where the driving & driven rotating surfaces momentarily rotate together without slippage.These CVTs can transfer substantial torque, because their static friction actually increases relative to torque throughput, so slippage is impossible in properly designed systems. Efficiency is generally high, because most of the dynamic friction is caused by very slight transitional clutch speed changes. The drawback to ratcheting CVTs is vibration caused by the successive transition in speed required to accelerate the element, which must supplant the previously operating and decelerating, power transmitting element.
Ratcheting CVTs are distinguished from VDPs and roller-based CVTs by being static friction-based devices, as opposed to being dynamic friction-based devices that waste significant energy through slippage of twisting surfaces. An example of a ratcheting CVT is one prototyped as a bicycle transmission protected under U.S. Patent 5,516,132 in which strong pedalling torque causes this mechanism to react against the spring, moving the ring gear/chainwheel assembly toward a concentric, lower gear position. When the pedaling torque relaxes to lower levels, the transmission self-adjusts toward higher gears, accompanied by an increase in transmission vibration.
6) Hydrostatic CVTs
Hydrostatic transmissions use a variable displacement pump and a hydraulic motor. All power is transmitted by hydraulic fluid. These types can generally transmit more torque, but can be sensitive to contamination. Some designs are also very expensive. However, they have the advantage that the hydraulic motor can be mounted directly to the wheel hub, allowing a more flexible suspension system and eliminating efficiency losses from friction in the drive shaft and differential components. This type of transmission is relatively easy to use because all forward and reverse speeds can be accessed using a single lever.An integrated hydrostatic transaxle (IHT) uses a single housing for both hydraulic elements and gear-reducing elements. This type of transmission, most commonly manufactured by Hydro-Gear[citation needed], has been effectively applied to a variety of inexpensive and expensive versions of ridden lawn mowers and garden tractors. Many versions of riding lawn mowers and garden tractors propelled by a hydrostatic transmission are capable of pulling a reverse tine tiller and even a single bladed plow.
One class of riding lawn mower that has recently gained in popularity with consumers is zero turning radius mowers. These mowers have traditionally been powered with wheel hub mounted hydraulic motors driven by continuously variable pumps, but this design is relatively expensive. Hydro-Gear, created the first cost-effective integrated hydrostatic transaxle suitable for propelling consumer zero turning radius mowers.
Some heavy equipment may also be propelled by a hydrostatic transmission; e.g. agricultural machinery including foragers, combines, and some tractors. A variety of heavy earth-moving equipment manufactured by Caterpillar Inc., e.g. compact and small wheel loaders, track type loaders and tractors, skid-steered loaders and asphalt compactors use hydrostatic transmission. Hydrostatic CVTs are usually not used for extended duration high torque applications due to the heat that is generated by the flowing oil.
The Honda DN-01 motorcycle is the first road-going consumer vehicle with hydrostatic drive that employs a variable displacement axial piston pump with a variable-angle swashplate.
7) Variable toothed wheel transmission
A variable toothed wheel transmission is not a true CVT that can alter its ratio in infinite increments, but rather approaches CVT capability by having a large number of ratios, typically 49. This transmission relies on a toothed wheel positively engaged with a chain where the toothed wheel has the ability to add or subtract a tooth at a time in order to alter its ratio relative to the chain it is driving. The "toothed wheel" can take on many configurations including ladder chains, drive bars and sprocket teeth. The huge advantage of this type of CVT is that it is a positive mechanical drive and thus does not have the frictional losses and limitations of the roller-based or VDP CVT’s. The challenge in this type of CVT is to add or subtract a tooth from the toothed wheel in a very precise and controlled way in order to maintain synchronized engagement with the chain. This type of transmission has the potential to change ratios under load because of the large number of ratios, resulting in the order of 3% ratio change differences between ratios, thus a clutch or torque converter is necessary only for pull-away. No CVTs of this type are in commercial use, probably because of above mentioned development challenge.
8) Single Tooth Cone CVT
A single tooth cone CVT is a non-friction CVT design. Like an iCVT a single tooth cone it also does not depend on friction to transmit torque; however, it does not have the weaknesses an iCVT has.The details of a Single Tooth Cone CVT can be found below:
- Single Tooth Cone CVT
9) Cone CVTs
A cone CVT varies the effective gear ratio using one or more conical rollers. The simplest type of cone CVT, the single-cone version, uses a wheel that moves along the slope of the cone, creating the variation between the narrow and wide diameters of the cone.The more sophisticated twin cone mesh system is also a type of cone CVT.
In a CVT with oscillating cones, the torque is transmitted via friction from a variable number of cones (according to the torque to be transmitted) to a central, barrel-shaped hub. The side surface of the hub is convex with a specific radius of curvature which is smaller than the concavity radius of the cones. In this way, there will be only one (theoretical) contact point between each cone and the hub at any time.
A new CVT using this technology, the Warko, was presented in Berlin during the 6th International CTI Symposium of Innovative Automotive Transmissions, on December 3–7, 2007.
A particular characteristic of the Warko is the absence of a clutch: the engine is always connected to the wheels, and the rear drive is obtained by means of an epicyclic system in output. This system, named “power split”, allows the engine to have a "neutral gear": when the engine turns (connected to the sun gear of the epicyclic system), the variator (i.e., the planetary gears) will compensate for the engine rotation, so the outer ring gear (which provides output) remains stationary.
10) Radial roller CVT
The working principle of this CVT is similar to that of conventional oil compression engines, but, instead of compressing oil, common steel rollers are compressed.For more details see EP1688645A1
Prototype applications for wind farms
Inside mechanical parts
The motion transmission between rollers and rotors is assisted by an adapted traction fluid, which ensures the proper friction between the surfaces and slows down wearing thereof. Unlike other systems, the radial rollers do not show a tangential speed variation (delta) along the contact lines on the rotors. From this, a greater mechanical efficiency and working life are obtained. The main advantages of this CVT are the manufacturing inexpensiveness and the high power efficiency.
Other Types׃
There must be a million ways to accomplish a continuously variable speed ratio, and many very creative minds have been at work developing new ones.
One especially unique example combines a planetary gear set with a gyroscope. The input power is divided between a planetary gear set and a gyroscope. The planetary gear set in turn divides the power between the gyroscope frame, forcing the gyroscope to precess, and the output shaft. As the gyroscope resists precession according to it's speed, at low gyroscope speeds, much of the power simply spins the gyroscope frame. However, the gyrosocope frame is arranged such that to precess, it must accelerate the gryoscope; as a result, the energy sent to the gyroscope is stored, rather than lost. This device, invented by Chris B. Hewatt, received patent 6,327,922 on November 10, 1999.
Another creative example uses a thick, flat, flexible belt running between two wheels. By pulling the belt tight against one wheel, the belt effectively increases it's radius, resulting in a change in speed ratio. Pulling the belt against the other wheel reverses the effect.
HOW DOES IT WORK?
Although there are different variations on the CVT theme, most passenger cars use a similar setup. Essentially, a CVT transmission operates by varying the working diameters of the two main pulleys in the transmission.
The pulleys have V-shaped grooves in which the connecting belt rides. One side of the pulley is fixed; the other side is moveable, actuated by a hydraulic cylinder. When actuated, the cylinder can increase or reduce the amount of space between the two sides of the pulley. This allows the belt to ride lower or higher along the walls of the pulley, depending on driving conditions, thereby changing the gear ratio. If you think about it, the action is similar to the way a mountain bike shifts gears, by "derailing" the chain from one sprocket to the next — except that, in the case of CVT, this action is infinitely variable, with no "steps" between.
The "stepless" nature of its design is CVT's biggest draw for automotive engineers. Because of this, a CVT can work to keep the engine in its optimum power range, thereby increasing efficiency and gas mileage. This translates to a gain of about 1-2 mpg, but as with any car, your mileage will vary based on your driving habits. A CVT can convert every point on the engine's operating curve to a corresponding point on its own operating curve.
With these advantages, it's easy to understand why manufacturers of high-mileage vehicles often incorporate CVT technology into their drivetrains.
Look for more CVTs in the coming years as the battle for improved gas mileage accelerates and technological advances further widen their functionality.
Take a look to this new transmission CVT design by BitRaptor. Is a continuously variable transmission CVT gear only (the only one functional in the world), very compact and lightweight, and which could replace the current systems both for efficiency, simplicity and not least the costs.
ReplyDeleteBecause this CVT work only with pinions is better the all other systems by efficiency and high torque transmission.
In the web page you will find more explanations, drawings and a short video of a basic prototype.
http://www.bitraptor.com/en_edyson_CVT.html
Other possible applications are bicycles, motorcycles, cars, automobils, boats, gearboxes, electric motors, steam and wind turbine, as well as a large number of industrial or agriculture applications whenever is necessary some adjustment of the gear ratio.
The current prototype demonstrate the high reliability and easy to manufacture. To increase the variation range of this systems can be connected in cascade.
Innovative aspects:
- The possibility to chose any ratio value without any interruption or jumps in the rotation.
- This gearbox variator CVT has the weight and complexity comparable to existing systems.
- Changes the transmission ratio in a continuous manner during operation, even when stationary.
- This gearbox variator system CVT, lightweight, compact and cheap (fully mechanical).
- Can be used as a real traction control without "cutting" the engine.
- Improved efficiency in the traditional combustion engines considerably improving the posivive ecological impact on large scale.
The first prototype will be ready for tests during this year.
Take a look to this new transmission CVT design by BitRaptor. Is a continuously variable transmission CVT gear only (the only one functional in the world), very compact and lightweight, and which could replace the current systems both for efficiency, simplicity and not least the costs.
ReplyDeleteBecause this CVT work only with pinions is better the all other systems by efficiency and high torque transmission.
In the web page you will find more explanations, drawings and a short video of a basic prototype.
http://www.bitraptor.com/en_edyson_CVT.html
Other possible applications are bicycles, motorcycles, cars, automobils, boats, gearboxes, electric motors, steam and wind turbine, as well as a large number of industrial or agriculture applications whenever is necessary some adjustment of the gear ratio.
The current prototype demonstrate the high reliability and easy to manufacture. To increase the variation range of this systems can be connected in cascade.
Innovative aspects:
- The possibility to chose any ratio value without any interruption or jumps in the rotation.
- This gearbox variator CVT has the weight and complexity comparable to existing systems.
- Changes the transmission ratio in a continuous manner during operation, even when stationary.
- This gearbox variator system CVT, lightweight, compact and cheap (fully mechanical).
- Can be used as a real traction control without "cutting" the engine.
- Improved efficiency in the traditional combustion engines considerably improving the posivive ecological impact on large scale.
The first prototype will be ready for tests during this year.
name vinod dhotre
ReplyDeletemo no-9260787165
full seminar report of cvt engine transmision