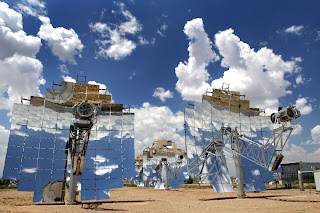
INTRODUCTION
A Solar Dish-Engine System is an electric generator that “burns” sunlight instead of gas or coal to produce electricity. The major parts of a system are the solar concentrator and the power conversion unit.
The dish, which is more specifically referred to as a concentrator, is the primary solar component of the system. It collects the solar energy coming directly from the sun (the solar energy that causes you to cast a shadow) and concentrates or focuses it on a small area. The resultant solar beam has all of the power of the sunlight hitting the dish but is concentrated in a small area so that it can be more efficiently used. Glass mirrors reflect about 92% of the sunlight that hits them, are relatively inexpensive, can be cleaned, and last a long time in the outdoor environment, making them an excellent choice for the reflective surface of a solar concentrator. The dish structure must track the sun continuously to reflect the beam into the thermal receiver.
The power conversion unit includes the thermal receiver and the engine/generator. The thermal receiver is the interface between the dish and the engine/generator. It absorbs the concentrated beam of solar energy, converts it to heat, and transfers the heat to the engine/generator. A thermal receiver can be a bank of tubes with a cooling fluid, usually hydrogen or helium, which is the heat transfer medium and also the working fluid for an engine. Alternate thermal receivers are heat pipes wherein the boiling and condensing of an intermediate fluid is used to transfer the heat to the engine.
SYSTEM DESCRIPTION
Dish/engine systems convert the thermal energy in solar radiation to mechanical energy and then to electrical energy in much the same way that conventional power plants convert thermal energy from combustion of a fossil fuel to electricity. As indicated in Figure 1, dish/engine systems use a mirror array to reflect and concentrate incoming direct normal isolation to a receiver, in order to achieve the temperatures required to efficiently convert heat to work. This requires that the dish track the sun in two axes. The concentrated solar radiation is absorbed by the receiver and transferred to an engine.
Dish/engine systems are characterized by high efficiency, modularity, autonomous operation, and an inherent hybrid capability (the ability to operate on either solar energy or a fossil fuel, or both). Of all solar technologies, dish/engine systems have demonstrated the highest solar-to-electric conversion efficiency (29.4%), and therefore have the potential to become one of the least expensive sources of renewable energy. The modularity of dish/engine systems allows them to be deployed individually for remote applications, or grouped together for small-grid (village power) or end-of-line utility applications. Dish/engine systems can also be hybridized with a fossil fuel to provide dispatchable power. This technology is in the engineering development stage and technical challenges remain concerning the solar components and the commercial availability of a solarizable engine.
The Following Describes the Components of Dish/Engine System
CONCENTRATORS
Dish/engine systems utilize concentrating solar collectors that track the sun in two axes. A reflective surface, metalized glass or plastic, reflects incident solar radiation to a small region called the focus. The size of the solar concentrator for dish/engine systems is determined by the engine. At a nominal maximum direct normal solar isolation of 1000 W/m2, a 25-Kw dish/Sterling system’s concentrator has a diameter of approximately 10 meters. The most durable reflective surfaces have been silver/glass mirrors, similar to decorative mirrors used in the home. Attempts to develop low-cost reflective polymer films have had limited success. Because dish concentrators have short focal lengths, relatively thin glass mirrors (thickness of approximately 1 mm) are required to accommodate the required curvatures. In addition, glass with low-iron content is desirable to improve reflectance. Depending on the thickness and iron content, silvered
Solar mirrors have solar reflectance values in the range of 90 to 94%.
The ideal concentrator shape is a paraboloid of revolution. Some solar concentrators approximate this shape with multiple, spherically shaped mirrors supported with a truss structure (Figure 1). An innovation in solar concentrator design is the use of stretched-membranes in which a thin reflective membrane is stretched across a rim or hoop. A second membrane is used to close off the space behind. A partial vacuum is drawn in this space, bringing the reflective membrane into an approximately spherical shape. Figure 2 is a schematic of a dish/Stirling system that utilizes this concept. The concentrator’s optical design and accuracy determine the concentration ratio. Concentration ratio, defined as the average solar flux through the receiver aperture divided by the ambient direct normal solar isolation, is typically over 2000. Intercept fractions, defined as the fraction of the reflected solar flux that passes through the receiver aperture, are usually Over 95%.
Tracking in two axes is accomplished in one of two ways, (1) azimuth-elevation tracking and (2) polar tracking. In azimuth-elevation tracking, the dish rotates in a plane parallel to the earth (azimuth) and in another plane perpendicular to it (elevation). This gives the collector left/right and up/down rotations. Rotational rates vary throughout the day but can be easily calculated. Most of the larger dish/engine systems use this method of tracking. In the polar tracking method, the collector rotates about an axis parallel to the earth’s axis of rotation. The collector rotates at a constant rate of 15º/hr to match the rotational speed of the earth. The other axis of rotation, the declination axis, is perpendicular to the polar axis. Movement about this axis occurs slowly and varies by +/- 23½º over a year. Most of the smaller dish/engine systems have used this method of tracking.
RECEIVERS
The receiver absorbs energy reflected by the concentrator and transfers it to the engine’s working fluid. The absorbing surface is usually placed behind the focus of the concentrator to reduce the flux intensity incident on it. An aperture is placed at the focus to reduce radiation and convection heat losses. Each engine has its own interface issues. Stirling engine receivers must efficiently transfer concentrated solar energy to a high-pressure oscillating gas, usually helium or hydrogen. In Brayton receivers the flow is steady, but at relatively low pressures. There are two general types of Stirling receivers, direct-illumination receivers (DIR) and indirect receivers which use an intermediate heat-transfer fluid. Directly-illuminated Stirling receivers adapt the heater tubes of the Stirling engine to absorb the concentrated solar flux. Because of the high heat transfer capability of high-velocity, high-pressure helium or hydrogen; direct-illumination receivers are capable of absorbing high levels of solar flux (approximately 75 W/cm). However, balancing the temperatures and heat addition between the cylinders of a multiple cylinder Stirling engine is an integration issue. Liquid-metal, heat-pipe solar receivers help solve this issue. In a heat-pipe receiver, liquid sodium metal is vaporized on the absorber surface of the receiver and condensed on the Stirling engine’s heater tubes (Figure 3). This results in a uniform temperature on the heater tubes, thereby enabling a higher engine working temperature for a given material, and therefore higher engine efficiency. Longer-life receivers and engine heater heads are also theoretically possible by the use of a heat-pipe. The heat-pipe receiver isothermally transfers heat by evaporation of sodium on the receiver/absorber and condensing it on the heater tubes of the engine. The sodium is passively returned to the absorber by gravity and distributed over the absorber by capillary forces. Stirling receivers are typically about 90% efficient in transferring energy delivered by the concentrator to the engine.
ENGINES
The engine in a dish/engine system converts heat to mechanical power in a manner similar to conventional engines, that is by compressing a working fluid when it is cold, heating the compressed working fluid, and then expanding it through a turbine or with a piston to produce work. The mechanical power is converted to electrical power by an electric generator or alternator. A number of thermodynamic cycles and working fluids have been considered for dish/engine systems. These include Rankine cycles, using water or an organic working fluid; Brayton, both open and closed cycles; and Stirling cycles. Other, more exotic thermodynamic cycles and variations on the above cycles have also been considered. The heat engines that are generally favored use the Stirling and open Brayton (gas turbine) cycles. The use of conventional automotive Otto and Diesel engine cycles is not feasible because of the difficulties in integrating them with concentrated solar energy. Heat can also be supplied by a supplemental gas burner to allow operation during cloudy weather and at night. Electrical output in the current dish/engine prototypes is about 25 kWe for dish/Stirling systems and about 30 kW for the Brayton systems under consideration. Smaller 5 to 10KW dish/Stirling systems have also been demonstrated.
a) Stirling Cycle
Stirling cycle engines used in solar dish/Stirling systems are high-temperature, high-pressure externally heated engines that use a hydrogen or helium working gas. Working gas temperatures of over 700oC (1292ºF) and as high as 20 MPa are used in modern high-performance Stirling engines. In the Stirling cycle, the working gas is alternately heated and cooled by constant-temperature and Constant volume process.
Thermal-to-electric conversion efficiencies of about 40%. Stirling engines are a leading candidate for dish/engine systems because their external heating makes them adaptable to concentrated solar flux and because of their high efficiency. All of the kinematic Stirling engines under consideration for solar applications are being built for other applications. Successful commercialization of any of these engines will eliminate a major barrier to the introduction of dish/engine technology.
b) Brayton Cycle
The Brayton engine, also called the jet engine, combustion turbine, or gas turbine, is an internal Combustion engine which produces power by the controlled burning of fuel. In the Brayton engine, like in Otto and Diesel cycle engines, air is compressed, fuel is added, and the mixture is burned. In a dish/Brayton system, solar heat is used to replace (or supplement) the fuel. The resulting hot gas expands rapidly and is used to produce power. In the gas turbine, the continuous and the expanding gas is used to turn a turbine and alternator.
As in the Sterling engine, recuperation of waste heat is a key to achieving high efficiency. Therefore, waste heat exhausted from the turbine is used to preheat air from the compressor. A schematic of a single-shaft, solarized, recuperated Brayton engine is shown in Figure 5. The recuperated gas turbine engines that are candidates for solarization have pressure ratios of approximately 2.5, and turbine inlet temperatures of about 850oC (1,562ºF). Predicted thermal-to-electric efficiencies of Brayton engines for dish/Brayton applications are over 30%. The commercialization of similar turbo-machinery for various applications by Allied Signal, Williams International, Capstone Turbines Corp., Northern Research and Engineering Company (NREC), and others may create an opportunity for dish/Brayton system developers.
ANCILLARY EQUIPMENT
ALTERNATOR:
The mechanical-to-electrical conversion device used in dish/engine systems depends on the engine and application. Induction generators are used on kinematic Stirling engines tied to an electric-utility grid. Induction generators synchronize with the grid and can provide single or three-phase power of either 230 or 460 volts. Induction generators are off-the-shelf items and convert mechanical power to electricity with an efficiency of about 94%.
Alternators in which the output is conditioned by rectification (conversion to DC) and then inverted to produce AC power are sometimes employed to handle mismatches in speed between the engine output and the electrical grid. The high-speed output of a gas turbine, for example, is converted to very high frequency AC in a high-speed alternator, converted to DC by a rectifier, and then converted to 60 hertz single or three-phase power by an inverter. This approach can also have performance advantages for operation of the engine.
COOLING SYSTEM:
Heat engines need to transfer waste heat to the environment. Stirling engines use a radiator to exchange waste heat from the engine to the atmosphere. In open-cycle Brayton engines, most of the waste heat is rejected in the exhaust. Parasitic power required for operation of a Stirling cooling system fan and pump, concentrator drives, and controls is typically about 1 kW.
CONTROLS:
Autonomous operation is achieved by the use of microcomputer-based controls located on the dish to control dish tracking and engine operation. Some systems use a separate engine controller. For large installations, a central System Control and Data Acquisition (SCADA) computer is used to provide supervisory control, monitoring, and data acquisition.
CURRENT ACTIVITIES
Thermal Motors (STM) to develop a dish/Stirling system for utility-scale applications. The SAIC/STM team successfully demonstrated a 20-kW unit in Golden, Colorado, in Phase 1. In December 1996, Arizona Public Service.
Company (APS) partnered with SAIC and STM to build and demonstrate the next five prototype dish/engine systems.
The overall objective is to reduce costs while maintaining demonstrated performance levels. The economic potential of dish/engine systems continues to interest developers and investors Next-generation hybrid receiver technology based on sodium heat pipes is being developed by Sun Lab in collaboration with industrial partners. Although, heat-pipe receiver technology is promising and significant progress has been made, cost-effective designs capable of demonstrating the durability required of a commercial system still need to be proven. Sun Lab is also developing other solar specific technology in conjunction with industry.
SYSTEM APPLICATION, BENEFITS, AND IMPACTS
Dish/engine systems have the attributes of high efficiency, versatility, and hybrid operation. High efficiency contributes to high power densities and low cost, compared to other solar technologies. Depending on the system and the site, dish/engine systems require approximately 1.2 to 1.6 ha of land per MW. System installed costs, although currently e over $12,000/kW for solar-only prototypes could approach $1,400/kW for hybrid systems in mass production. This relatively low-cost potential is, to a large extent, a result of dish/engine system’s inherent high efficiency.
UTILITY APPLICATION
Because of their versatility and hybrid capability, dish/engine systems have a wide range of potential applications. In principle, dish/engine systems are capable of providing power ranging from kilowatts to gigawatts. However, it is expected that dish/engine systems will have their greatest impact in grid-connected applications in the 1 to 50 MW power range. The largest potential market for dish/engine systems is large-scale power plants connected to the utility grid. Their ability to be quickly installed, their inherent modularity, and their minimal environmental impact make them a good candidate for new peaking power installations. The output from many modules can be ganged together to form a dish/engine farm and produce a collective output of virtually any desired amount. In addition, systems can be added as needed to respond to demand increases. Hours of peak output are often coincident with peak demand. Although dish/engine systems do not currently have a cost-effective energy storage system, their ability to operate with fossil or bio-derived fuels makes them, in principal, fully dispatchable. This capability in conjunction with their modularity and relatively benign environmental impacts suggests that grid support benefits could be a major advantage of these systems.
REMOTE APPLICATION
Dish/engine systems can also be used individually as stand-alone systems for applications such as water pumping. While the power rating and modularity of dish/engine systems seem ideal for stand-alone applications, there are challenges related to installation and maintenance of these systems in a remote environment. Dish/engine systems need to stow when wind speeds exceed a specific condition, usually at about 16 m/s. Reliable sun and wind sensors are therefore required to determine if conditions warrant operation. Intermediate-scale applications such as small grids (village power) appear to be well suited to dish/engine systems. The economies of scale of utilizing multiple units to support a small utility, the ability to add modules as needed, and a hybrid capability make the dish/engine systems ideal for small grids.
HYBRIDIZATION
Because dish/engine systems use heat engines, they have an inherent ability to operate on fossil fuels. The use of the same power conversion equipment, including the engine, generator, wiring, and switch gear, etc., means that only the addition of a fossil fuel combustor is required to enable a hybrid capability. For dish/Brayton systems, addition of a hybrid capability is straightforward. A fossil-fuel combustor capable of providing continuous full-power operation can be provided with minimal expense or complication. The hybrid combustor is downstream of the solar receiver, and has virtually no adverse impact on performance. In fact, because the gas turbine engine can operate continuously at its design point, where efficiency is optimum, overall system efficiency is enhanced. System efficiency, based on the higher heating value, is expected to be about 30% for a dish/Brayton system operating in the hybrid mode. For dish/Stirling systems, on the other hand, addition of a hybrid capability is a challenge. The external, high temperature, isothermal heat addition required for Stirling engines is in many ways easier to integrate with solar heat than it is with the heat of combustion. Although, the cost of these systems is expected to be much less than a continuously variable hybrid receiver, their operational flexibility will be substantially reduced. System efficiency, based on higher heating value, is expected to be about 33% for a Dish/Stirling system operating in the hybrid mode.
ENVIRONMENTAL IMPACTS
The environmental impacts of dish/engine systems are minimal. Stirling engines are known for being quiet, relative to internal combustion gasoline and diesel engines, and even the highly recuperated Brayton engines are reported to be relatively quiet. The biggest source of noise from a dish/Stirling system is the cooling fan for the radiator. There has not been enough deployment of dish/engine systems to realistically assess visual impact. The systems can be high profile, extending as much as 15 meters above the ground. However, aesthetically speaking they should not be considered detrimental. Dish/engine systems resemble satellite dishes which are generally accepted by the public.
Emissions from dish/engine systems are also quite low. Other than the potential for spilling small amounts of engine oil or coolant or gearbox grease, these systems produce no effluent when operating with solar energy. Even when operating with a fossil fuel, the steady flow combustion systems used in both Stirling and Brayton systems result in extremely low emission levels. This is, in fact, a requirement for the hybrid vehicle and cogeneration applications for which these engines are primarily being developed.
RESEARCH AND DEVELOPMENT NEEDS
The introduction of a commercial solar engine is the primary research and development (R&D) need for dish/engine technology. Secondary R&D needs include a commercially viable heat-pipe solar receiver for dish/Stirling, a hybridreceiver design for dish/Stirling, and a proven receiver for dish/Brayton. All three of these issues are currently being addressed by Sun Lab and its partners, as part of the DOE Solar Thermal Electric Program. In addition, improvement in dish concentrator components, specifically drives, optical elements, and structures, are still needed and are also being addressed, albeit at a low level of effort. The solar components are the high cost elements of a dish engine system, and improved designs, materials, characterization, and manufacturing techniques are key to improving competitiveness. Systems integration and product development are issues for any new product. For example, even though MDA successfully resolved many issues for their system, their methods may not apply or may not be available to other designs. Issues such as installation logistics, control algorithms, facet manufacturing, mirror characterization, and alignment methods, although relatively pedestrian, still need resolution for any design. Furthermore, if not addressed correctly, they can adversely affect cost. An important function of the Joint Ventures between Sun Lab and industry is to address these issues.
ADVANTAGES:
1. Solar dish-engine systems are being developed for use in emerging global markets for distributed generation, green power, remote power, and grid-connected applications.
2. High efficiency, versatility and “conventional” construction.
3. Individual units, ranging in size from 9 to 25 kilowatts.
4. Can operate independent of power grids in remote water or to provide electricity for people living in remote areas sunny locations to pump.
5. Land requirements for dish/engine systems are approximately 1.2-1.6 ha/MW.
6. No water is required for engine cooling. In some locations, a minimal amount of water is required for mirror washing.
DISADVANTAGES
1. High Initial costs.
2. Sun intensity decrease due to variance in sunlight such as seasonal changes, cloud, fog, and pollution.
CONCLUSIONS
Because of their versatility and hybrid capability, dish/engine systems have a wide range of potential applications. In principle, dish/engine systems are capable of providing power ranging from kilowatts to gigawatts. However, it is expected that dish/engine systems will have their greatest impact in grid-connected applications in the 1 to 50 MW power range. The largest potential market for dish/engine systems is large scale power plants connected to the utility grid. Their ability to be quickly installed, their inherent modularity, and their minimal environmental impact make them a good candidate for new peaking power installations. The output from many modules can be ganged together to form a dish/engine farm and produce a collective output of virtually any desired amount. In addition, systems can be added as needed to respond to demand increases. Hours of peak output are often coincident with peak demand. Although dish/engine systems do not currently have a cost-effective energy storage system, their ability to operate with Fossil or bio-derived fuels makes them, in principal, fully dispatch able. This capability in conjunction with their modularity and relatively benign environmental impacts suggests that grid support benefits could be a major advantage of these systems.
This project can provide us as a better alternative in order to cope up with the increasing demand of power as a cheaper and renewable source over the fossil fuels which are on the verge of extinction.
sanagani sreedhar, email id:sreedhar.0201@gmail.com, EEE
ReplyDelete