The industrial revolution in the 18-century brought about the upliftment of Science & Technology. The revival of learning showed a new way of life the world in various spheres. Since then the industries have made a lot of progress. The industries have made a history in the world and since then they are progressing with leaps and bounds. In India, industries during that time were small ones.
The British were afraid that in case the India come to know "The Know How" of various industries then the British economy, would have lessened there by bringing about the decline of the British Empire in India.
The British were afraid that in case the India come to know "The Know How" of various industries then the British economy, would have lessened there by bringing about the decline of the British Empire in India.
After Independence India has made such a remarkable progress in the industries that it becomes necessary to mention that the India intelligence has proved its worth and the labors has also contributed a lot towards the progress, The Indian Industries can now compete in the world. The industries have helped India to have good trade with the other countries and have earned a good amount of foreign exchange there by raising the economic standards and making way of India to become self sufficient and self reliant.

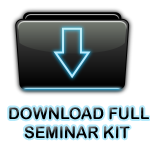
INTRODUCTION
1.1 GENERAL
The H.M.T. Ajmer previously called as Machine Tools Corporation of India Ltd., which was incorporated in January. 1967 to set-up a Grinding Machine Tools Plant at Ajmer to specialize in the Manufactures, development and Marketing of high precision and sophisticated grinding machine tools, which are urgently required for our rapidly development national economy. It was installed as a branch of H.M.T. under the technical collaboration with TOS Hitivar, Czechoslovakia.
It was commencing its production with a small but highly versatile universal tool post Grinder "MTC" Model (ITG-15a) in the year 1970. The factory has been able to progressively tools like Universal Tools & Cutter Grinder "MTC" Model (GTC - 28), Crankshaft Grinding "MTC" Model (GCS-500), Vertical Surface Grinder "MTC" Model (GVS-30), Internal Grinder "MTC" Model (GIF-80) and Center less Grinding Machine. However it has started the production of centre lathe of various sized also.
The H.M.T. Ajmer has its own design & development in which new designs are being development to cover requirements of small scale as well as specialized industries such as Ball & Roller Bearing Industry.
It has a well developed machining and inspecting facilities and a most modern Tools room where Jigs and fixture and tools are manufacture to very standards comparable with the best in world
1.2 HMT MACHINE TOOLS LTD., AJMER
1.2.1 Profile
The Unit was established at Ajmer as "MACHINE TOOL CORPORATION OF INDIA LIMITED." Government of India was undertaking in January, 1967 with the collaboration of Czechoslovakian M/s. Skoda export and M/s.WMW, GDR then the East Germany. For the
purpose of making India self-reliant in manufacture of precision grinding machines this unit was merging with M/s. HMT Limited in 1975.
From 1.4.2000 as per the turnaround plan, approved by the Govt. of India, it became a unit of HMT MACHINE TOOLS LTD., which is wholly owned subsidiary of nation's prestigious company, HMT LIMITED. This unit is situated over 178 acres of land, out of which 68 acres are for factory campus and 116 acres for a beautiful township comprising 136 quarters for housing its employees with community centre, club, playground, etc.
1.2.2 Technological Base
The unit is well equipped with modern machine shops having 200 nos. of different types of precision machines, such as, CNC machining centers, CNC lathes, high precision jig boring machines, high precision cylindrical grinders and slide way grinders, besides well equipped heat treatment Shop, measuring centre, material testing laboratory, CAD centre for design & development and foundry. Unit has also captive power generation capacity of 1850 KVA to meet power shortage.
Ajmer unit is capable to meet the requirements of all types of grinding machine tools for India as well as world market including CNC, tooled-up machines & special purpose machines tailor made to customer’s requirement.
The unit has highly skilled and dedicated work force and has strength of qualified & experienced engineering personnel to fulfill requirement of business operations to the satisfaction of customers.
1.2.3 Unit Business
1.2.3.1 Manufacture of Machine Tools
1. Wide range of CNC, Conventional General Purpose & Special purpose Grinding machines (cylindrical, center less, internal, horizontal and vertical, tool and cutter).
2. Unit's product CNC Double Disc Grinder displayed in IMTEX'1988 at New Delhi was conferred upon CMTI-Trust award for the best innovative design of the year.
1.2.3.2 Reconditioning of Machine Tools.
All types of Grinding Machines.
1. CNC Turning Centers.
2. CNC Training Machines (Lathe & Machining Centre).
3. Other Machine Tools
4. Conversion of old machines into CNC machines & retrofitting of CNC control on conventional machines.
1.2.3.3 Job Orders/Customer Component Manufacture
1. Hydraulic Groups for Defense.
2. Hydraulic Lifts for Tractors.
3. High Precision Components/operations on job work basis for Automobile Industry and BHEL.
4. Jigs & Fixtures
5. Wiping Cylinders for Bank Note Press Supply of castings
1.2.3.4 Other Services offered
1. Manufacture of Jigs, Fixtures, Tooling’s,
2. Manufacture of Hydraulic Group for Defense. Hydraulic Assembly for Tractors.
Manufacture of High Precision & critical items, assemblies.
3. Reconditioning of old machines.
4. Supply of castings.
5. Training to outsiders/customers.
6. Chemical, Mechanical & Metrological Tests, Checking & Calibration
1.3 Productivity & Quality
Great emphasis is given on Productivity and Quality in HMT. The Unit has achieved substantial progress in implementation of productivity improvement activities. KAIZEN, ISO-9000, Total Customer Satisfaction, TQM, Multi-trade training, Good House Keeping through 5-S, Waste Elimination and Small Group Activities etc
The Unit has the distinction of getting "National Productivity Award" (instituted by National Productivity Council of India), in Machine Tool Category for the year 1986-87 from the Honorable President of India.
1.4 LOCATION & HISTORY
The H.M.T. Ajmer is situated near Ajmer Dairy 6 Km. from Ajmer City of Ajmer-Beawar Road. Its foundation stone was laid on December 16, 1966 and production was started in 1970. It produced various types of Grinding Machine, Lathe Machines of various sizes. The product of H.M.T., however could not orient the local market towards them due to tough competition but they have nicely attached the foreign market. The H.M.T. was highly appreciated by Foreign Experts in many industries trade fair organized in India and Abroad.
1.4.1 H.M.T. (H.M.T. Machine Tools)
Hindustan Machine Tools is a public sector undertaking it was setup as Bangalore and registered in Feb. 1953.
It is one of the ten largest manufactures of machine tools in the world.
1.4.2 Marketing
H.M.T. has a type marketing network throughout the country. While each business group has a central marketing division, each factor has also a unit Sales Department.
SAFETY MEASURES
2.1 SAFETY MEASURES
1. Do not wear loose garments they got caught leading to accidents.
2. Either roll up your uniform releases or bottom up the cuffs.
3. Always wear uniform and shoes they are for your safety.
4. Long and unruly hair is always dangerous particularly when working near rubbing parts or machines or cutters.
5. Ring, bracelets and watches can get caught in the machinery. Do not wear them when on duty.
6. Be calm and patient while working. A disturbed mind will invite trouble and haste makes waste.
7. While walking watch your steps.
8. Be watchful of blind corners, you may be caught in the wrong way.
9. Do not ailment the attention of others or do not got yourself alleviated by other while working.
10. Don't carry to many tools/instruments.
11. Put the work area clean dry clip free and free of obstructions.
12. Watch out for jobs, brass, rods, etc. which protrude form for vice and machines it my hit you resulting in accident.
13. Use personal protective equipment and safety drives.
14. Do not touch/operate equipment unless you are authorized.
15. Do not leave on the machine.
16. Lubricate the Machine as is required
17. Do not clean the machine parts with hearts, bars use cloth, cotton, wash brush.
18. Do not repair or try to adjust or repair any equipment when in motion.
19. Ensure all machine controls of the machine are accessible to you.
20. Do not attempt to change the speed of the machine when in motion.
21. Don’t keep unwanted instruments/tools on the machine bed.
22. Use the right tools for the right join the right way.
23. Use the proper speed.
24. Use the proper feed.
25. Use the proper depth of cut
26. Do not use broke or blunt or damaged tools.
27. Do not walk or work under suspended loads.
28. Do not blow air from your mount to clean the components.
29. Keep yourself at a safe distance from the cutting tool in motion.
30. Don’t touch with pressure the job when it is hot or in motion.
31. Switch off machine immediately in anything goes wrong.
32. For any injury whether small or big got first aid first.
FOUNDRY & PATTERN SHOP
3.1 FOUNDRY & PATTERN SHOP
In a foundry shop casting of different jobs is prepared by using the moulding box, pattern and molding materials-
3.1.1 Molding material
(1) Green sand
(2) Dry sand
(3) Semi Bake sand
(4) Bake sand
(5) No bake sand
3.1.2 Binding material
Part – B Chemical
Part – C Setting
3.1.3 Preparation of Sand – All of first fresh silica sand and bake sand are mixed in definite ratio (50&50%) in the Muller. Some binding material and some other material are also mixed in the sand. This mixture is known as molding sand.
3.1.4 Preparation of a mould –
Following elements are used for preparing a mould.
(1) Pattern
(2) Molding box
(3) Molding sand
(4) Face plate
(5) Split plat
(6) Matching pins etc.
3.2 PROCEDURE
A prepared pattern is placed on the face plate and molding boxes also fixed. Now molding sand is filled in molding boxes. Now this mould sand is pressed by manually and also by machine for the good packing of molding sand. This process is known as reaming process.
After reaming process and complete molding, boxes are kept in oven. Here sand packing takes place. So there is no damage in cores and edges. Heating process is done at 220o C for 2 hours
3.2.1 Closing of boxes
After hearing process, cope and drag are clamped and some packing material also used for good packing of boxes.
3.2.2 Pouring of metal
The melted metal is poured in the boxes through the sprue cup. The melted metal fills in cavities through the runner and gate ways. When the cavity is filled by melted metal, it comes out from riser. The shrinkage of melting metal in cavity is filled by the metal which is in the riser. The molding boxes are cooled in air for one day and then opened and molding job is come out.
3.3 ACCESSORIES
a. Chills – Chills are provided in the molding at the places where more hardness is required in the casting. These are iron plates.
b. Chaplet – Chaplet are provided in the gaps to maintain the gaps.
3.4 FURENACE
Induction Furnace is used for melting the metal. There is tilting head in furnace for pour out the melting metal. To get more special properties following metal is added.
(a) Ferro Manganese
(b) Ferro Silicon
(c) Ferro chromium
(d) Carbon (as required)
(e) To remove slag from the melting metal silica sand is mixed in the furnace.
To get more fluidity of metal Elion cline mixed in the melted metal.
Chemical Name – Calcium Sal site.
MANUFACTURING DEPARTMENT
4.1 INTRODUCTION
In all the factories, manufacturing department is main department, because here product or different parts of machine is prepared.
H.M.T. Ajmer also has a manufacturing dept. , Which is divided in the following sections.
1. Mfg. H.P. (Heavy Parts)
2. Mfg. S.P. (Small Parts)
In manufacturing H.P. heavy parts of an m/s like machine bed, gear box main body etc. are manufacture.
In manufacturing S.P. different small components and parts of machine like shaft, spindle, gear, bushes, screw etc. are manufacture.
Following sections comes in the small part manufacturing department.
1. Non round section
2. Round Section
3. Spindle, shaft Section
4. Gear Section
5. Heat Section
6. M.M.S. (Medium Machine Shop)
7. Special accessories & spindle Assembly
4.2 ROUND SECTION
Here small rounded components are manufacture. Following m/c are used to manufacture the round parts.
Name of machine No. off Type
1. Capstan Lathe 1
2. Drum Turret Lathe 1 RTV50
3. Turret Lathe 2
4. Centre Lathe 6
5. Drilling machine 1
6. Radial Drilling machine 1
7. Centre less Grinding machine 1 GCL60
8. Cylindrical grinding machine 1 K130U
9. K-130 Grinding machine 1
10. Horizontal Milling machine 1
11. Vertical Milling machine 1
12. Slotting machine 1 CH-25
4.3 MEDIUM MACHINE SHOP
Knee Type Milling Machine FN2/FN3
4.3.1 Salient Features:
1. Streamlined construction, rugged and vibration free.
2. 7.5/5l5 kW Motor for heavy stock removal.
3. Power operated feeds and rapid traverses in all directions.
4. Independent main drive and feed drive motors.
5. Wide range of spindle speeds and feeds.
6. Instantaneous braking of spindle and table drives through electromagnetic clutches.
7. High rate of rapid traverses.
8. Light fingertip push button controls.
9. Inching push button for speed and feed drives.
4.3.2 Specifications:
FN3/FN3E FN3/FN3E FN2/FN2E
(H & V) (U) (H, U, V)
Overall dimensions mm 2050*355 2060*300 1520*310
(L*W)
Clamping area mm 1600*355 1600*300 1350*310
(L*W)
Power operated table traverses
Longitudinal mm 1200 950 800
Cross mm 320 320 265
Vertical mm 425 375 400
Maximum safe weight kg 600 400 350(H&V)
On table 250(U)
15.
Number of speeds 18 18 18
Speed range rpm 25.5-1800 35.5-1800 35.5-1800
Main motor kW/rpm 7.5/1500 7.5/1500 5.5/1500
Feed motor kW/rpm 3.7/3000 3.7/3000 1.5/1500
Space required mm 386*253*214(H) 345*253*209 255*250*207(H)
(L*B*H) 386*206*217(V) 255*196*197(V)
Packing case cm 260*245*230 260*245*230 230*195*210
(L*W*H)
Weight (net/gross) kg 3600/4500(H) 3700/4600 2400/3200(H)
3700/4600(V) 2500/3300(V&U)
4.4 Milling Machine FNR
4.4.1 Salient Features:-
1. Streamlined construction, rugged and vibration free
2. 5.5 kW motor for heavy stock removal
3. Power operated feeds and rapid traverses in all direction
4. Independent feed drive motor
5. Wide range of spindle speeds and feeds
6. Speeds up to 1800 rpm and feeds up to 800 mm/min.
7. All operations controlled with effortless ease by push buttons
8. ‘Inching’ push button for speed and feed drives
4.4.2 Main Data:-
Horizontal Vertical
Table size clamping area mm 1350x310 1350x310
(length & width)
Powered operated mm 800 800
(table traverses)
Longitudinal traverse
Cross mm 265 265
Vertical mm 400 400
Main motor kW 5.5 5.5
This section consists of basically CNC operated machine. There are three machines in this section capable of doing several operations in one complete cycle. Two of the machines are HMC (Horizontal machine centre) and one is VMC (Vertical machining centre).
Each tool with its collect chuck gets attached to spindle before operation.
VMC Vertical M/C centre at Pinjore unit.
HMC Horizontal M/C centre.1. In KTM, London 2. In HMT, copied of KTM in Hyderabad unit
4.5 HEAVY PARTS SECTION
Heavy Parts section Deals with the parts having greater dimensions. All the bed of different castings are dealt here along with other heavy castings. The process plan here starts with the marking three basic equipments are used viz. Tri-square, Height gauge & Surface plate. The marking is done to pave the way of casting for other operations. After marking planning is done on a huge machine called as Double Housing Plano- Milling Machine. The machine is capable of having four cuts in a single pass. After planning drilling, boring etc. are done. Before marking, the priming is done which gives two advantages. First - The Consumption of paint will be less while painting. And second - The marking will become visible.
4.6 CNC 3-Axes Plano milling Machine
4.6.1 Salient Features:
1. Twin column machine with vertical ram.
2. Ideal for medium & large size components.
3. All five faces of a component can be machined with a right angle attachment.
4. Siemens 840D control system.
5. Auto attachment pick up and auto indexing of right angle head.
6. 60-Tool ATC.
7. All sides fitted with LM guides.
8. Universal milling attachment (optional)
4.6.2 Specifications:-
Table mm 2000*5000
Width between columns mm 2600
Height of vertical spindle face mm 400/1500
From table top-Min. /Max.
Horizontal spindle axis (ram) mm 150/1235
Transverse- X/Y/Z min 5200/4200/1100
Rapid transverse-X/Y/Z mm/min 7000/10000/500
Spindle speed rpm 30-3000
Spindle power kW 22
TRACTOR HYDRAULIC
5.1 TRACTOR HYDRAULIC
Hydraulic lift system – (Used in tractor for lifting)
5.1.1 Introduction – It is a system which used to lift the weight (trolleys and ploughs) by using the pressurized hydraulic oil.
5.1.2 Construction – The important component of the system are as follows:-
1. Housing
2. Distributor
3. Cylinder piston and connecting rod
4. Main shaft
5. Torsion shaft
6. Lever with cam
Hydraulic lift assembled with 220 parts
5.1.3 Distributor – It is the heart of hydraulic lift system as it control fluid flow direction. It consists of integrated lines and also consist with I.C., O.C. and D.V. Bush.
It has one inlet and out let opening. It received pressurized oil from pump and send it to the cylinder by U-connection.
5.1.4 Working
When pressurized oil enters cylinder it displace the piston in forward direction piston connected to the lever with connecting rod. So when piston moves in forward direction leaver rotate. Leaver connected to the main shaft by splint system so it rotate the mainshaft.
Arms connected to the main shaft so it lift the arms and weight connected with arms so arms also lifting the Wright
5.1.5 Hydraulic Lift Testing - Hydraulic lift testing is done by hydraulic lift testing machine. There is some standard parameter tested on testing machine which are as follows –
(a) Setting parameter-
1. Pressure – 120 kg s/cm2
2. Discharge – 20 Lt./min.
(b) Testing parameter –
(a) Lifting time – 2 - 2.25 Sec. at 20 Lt./min.
(b) Lifting position – 80 from top lift position
(c) Lifting and down movement – Should be jerk free, regular, no dropping. Sinking
Problems – In hydraulic lift
1. Not lifting the weight
2. Not coming down
3. Sinking
4. Jerking
Machine's which used to make the hydraulic parts in hydraulic work shop are following in –
1. GIF – 100 s (internal facing grinder)
2. IGE – 9
3. G – 131
HYDRAULIC CYLINDRICAL GRINDER G17/22
6.1 Salient Features:
1. Designed for high rates of stock removal for batch production requiring fine tolerance limits with finest surface finish.
2. A single lever controls table traverse, work rotation, coolant flow and rapid approach of Available in universal and production models, having infinitely variable table traverse, with a dwell and automatic in feed at table reversals.
3. The universal models are equipped with swiveling wheel head and built-in provision for internal grinding.
4. Wheel head during production runs.
6.2 Specifications:
G17/800 G17/2000 G22/2000
Center height mm 175 175 225
(225 with G22 setup) (225 with G22 setup)
Maximum grinding diameter mm 250 250 250
Swing over bed mm 350 350
(450 with G22 setup) (450 with G22 setup) 450
Distance between centers mm 800 1200 2000
Speed (infinitely variable m/min. 0.05-5 0.05-5 0.10-4
Grinding wheel diameter
(Max./Min.)
U model mm 450/320 450/320 450/320
P model mm 500/360 500/360 500/360
Speed
U model rpm 1060/1320 1060/1320 1060/1320
P model rpm 960/1150 960/1150 960/1150
Grinding wheel motor kW 5.5 5.5 5.5
CNC DOUBLE DISC GRINDING MACHINE GDS 15/22
7.1 Salient Features:
1. Ideal grinder for mass production of components having two flat and opposite parallel surfaces with higher geometrical accuracies.
2. Machines up to 4-axes CNC control.
3. User-friendly grinding cycles by customized screen (picot programming).
4. Preloaded antifriction guide ways for precise positioning and rigidity.
5. Super precision antifriction bearings for grinding spindles.
6. Direct driven ball screws with AC digital servomotors for linear axes.
7. Hydraulic swing arm dresser.
8. Automatic centralized lubrication system.
9. Free-standing electrical panel and hydraulic power pack.
10. Pendant type operator panel.
11. Built-in safety interlocks.
12. Input resolution 0.0001 mm
7.2 Special Executions:
1. Variable speed drives for grinding wheels suitable for different areas on opposite surfaces.
2. Machine can be equipped with rotary feeder, through feeder, rotary magnetic plate through feeder, reciprocating feeder, swivel arm feeder, oscillating feeder as per requirement.
3. Diamond wheels.
4. Post-process gauge.
5. Wheel positioned for grinding wheel.
7.3 Specifications:
CNC GDS 15 CNC DGS 22
Grinding wheel size (OD*W) mm 400/450/500*65 585/660/762*70/80
Peripheral/cutting speed m/sec 30 30
Dressing distance mm 80 200
Grinding wheel motor kW 11/15 18.5/22/37
Spindle speed of both wheels rpm 1000 900
Dressing distance between
Wheels mm 80 200
Rotary feeder capacity
(Job diameter) mm 10-50 20-80
Rotary feeder capacity
(Thickness) mm 3-30 3-40
Through feeder
(Job outer diameter) mm 20-70 35-220
CNC CYLINDRICAL GRINDING MACHINE G12
8.1 Salient Features
1. CNC cylindrical Grinding Machine with angular wheel head/straight wheel head facility
2. High rapid traverse for slides
3. Rigid structure
4. Well ribbed cast iron bed
5. Wheel spindle supported on multi lobbed hydrodynamic bearings
6. Turcite pasted table guide ways
7. Preloaded antifriction guide ways for X-axis (wheel head slide) to have high positioning accuracy
8. Work head spindle mounted on preloaded ball bushings for axial movement of the spindle through electromechanical drive
9. Tailstock quill mounted in preloaded ball bushings with manual taper correction
10. CNC dresser (2 axes) driven by DC servomotors
11. Moving weight type in situ balancing equipment
12. Air blast oil cooler/ refrigerating type, to maintain temperature of lubrication oil
13. Automatic wheel slide retraction facility during power failure
14. 3 axes CNC system Sinumerik 810G/Hinumerik 3G.
8.2 Optional Features
1. Refrigeration type oil cooler to control the temperature of lubrication oil, with reference to ambient.
2. AC servo motors in place of DC servo motors
3. DC motor for work head/wheel head
4. Paper band cum magnetic separator for fine filtration of coolant
Built-in quality, excellent, performance, flexible machine with high power, speed and accuracy for increased productivity.
Ideal for Auto, ancillaries, Defense and General Engineering Industries.
9.1 DESIGN CHARATERISTICS
1. 45 degree slant bed for efficient chip & coolant management.
2. LM guide ways for both the Axes for precise positioning and rigidity.
3. Directly Driven Ball screws with high response AC digital servo drive.
4. High acceleration rate minimizes idle time during machining.
5. Spindle supported on Precision Angular contact Ball bearings of consistent accuracies.
6. 8- Station Bi-directional electromechanical turret.
7. Power chucks Diameter 200 (250) mm. Hydraulic actuation of quill.
8. Integrated hydraulics an Electricals for PLUG & START facility.
CNC TURNING CENTER STALLION 200
Latest breed of CNC Turning Centers offering economical solution for production of high precision turned parts
1. 30o Slant saddle.
2. 8-Station bi-directional turret.
3. Programmable tailstock.
4. Optional C-axis and driven tools.
5. Hardened and ground integral guide ways.
6. Single piece monolithic cast iron bed base structure.
7. Direct coupled servomotors.
8. Large cross section chip chutes for easy chip flow.
10.1 Specifications
Swing over bed mm 460
Maximum turning diameter mm 250
Maximum turning length mm 600
Bar passage/Spindle bore mm 53
Chuck diameter mm 250
PRECISION CENTERLESS GRINDING MACHINE GCL 60/100/140
11.1 Salient Features:
1. Bed made of high tensile strength cast iron, heavily ribbed for better vibration damping and shock absorption.
2. Grinding wheel spindle mounted on special tilting pad type hydrodynamic bearings.
3. Regulating wheel spindle mounted on super precision antifriction bearings for higher rigidity.
4. Faster & easy wheel change due to cantilever design spindle.
5. Automatic separate lubrication system for grinding wheel head spindle.
6. Outboard support provided for better rigidity in GCL 140.
7. Electrically operated micron impulse feed for size correction and rapid movement of infeed slide for faster setting (except GCL 60).
8. GCL 60 - a compact machine suitable for batch & mass production.
9. Auto plunge grinding optional in GCL 60.
11.2 Specifications:-
GCL60 GCL100 GCL140
Center height mm 975 1100 1160
Grinding diameter-Min. / Max. mm 1.5/63 3/100 3/140
Maximum length through feed mm 220 320 370
grinding without feeding equipment
Maximum length in feed grinding mm 95 195 245
Grinding wheel size (OD*W) mm 350*100 500*200 500*250
Peripheral / cutting speed m/sec 33 33
(45 optional) (45 optional)
Grinding wheel motor kW 7.5 22 22
(30 optional) (30 optional)
Grinding wheel speed rpm 20-350 20-200 20-120/250
(Infinitely variable)/
Dressing speed
Girnaralloys is a leading Manufacturers & Exporters of Austenitic ductile iron castings, Machined castings India, Ni hard, Ni-hard, Ni resist, Ni-resist, Alloy Steel Castings Manufacturers in India.
ReplyDeleteYour blog is really helpful. I am also making a hexapod machine too. I am just wandering the way you control the six servos. Could you please send me the code? I will definitely appreciate that.
ReplyDeleteBuy CNC Machine